- Home
- Corporate information
- History
- Development history
Development history
Cataler has been developing various technologies for half a century, from pellet-type exhaust gas purification catalysts, to electrocatalysts for fuel cell electric vehicles. Please see the development history of our products and technologies that have been used in many products such as automobiles and motorcycles.
Development history
Cataler has been developing various technologies for half a century, from pellet-type exhaust gas purification catalysts, to electrocatalysts for fuel cell electric vehicles. Please see the development history of our products and technologies that have been used in many products such as automobiles and motorcycles.
2010sdevelopment history
Fuel cell electrocatalyst for electric vehicles
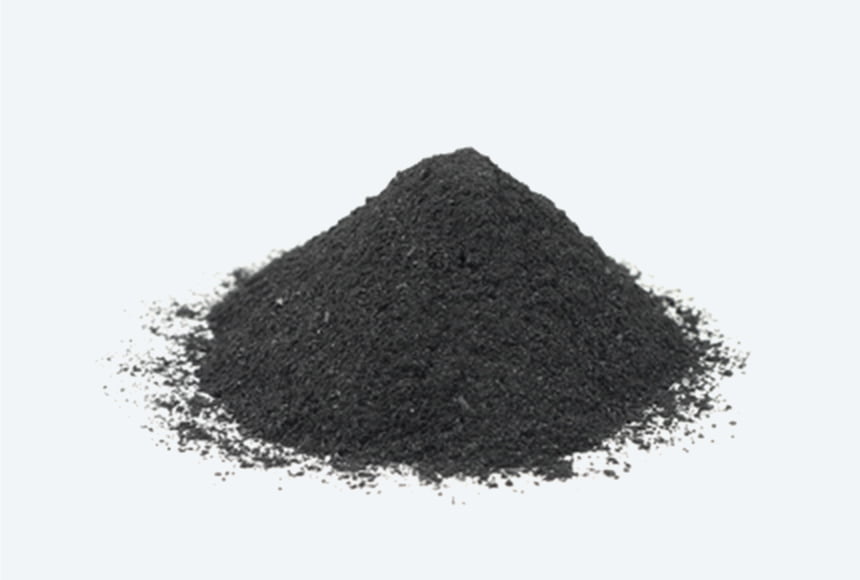
In December 2014, Toyota Motor Corporation launched the fuel cell electric vehicle (FCEV), which is the ultimate eco-car that does not emit any carbon dioxide (CO2). The world's first mass-produced FCEV "MIRAI" was equipped with the Cataler's electrocatalyst for fuel cell electric vehicles. In the electrocatalyst developed by Cataler, by high dispersing nanometer platinum (Pt) and cobalt (Co) alloy particles on a carbon material. The reactivity of hydrogen (H2) and oxygen (O2) was very high and we could reduce Pt amount. We contributed greatly to the performance progress and cost reduction for MIRAI.
Awards
- 2021
- 2015
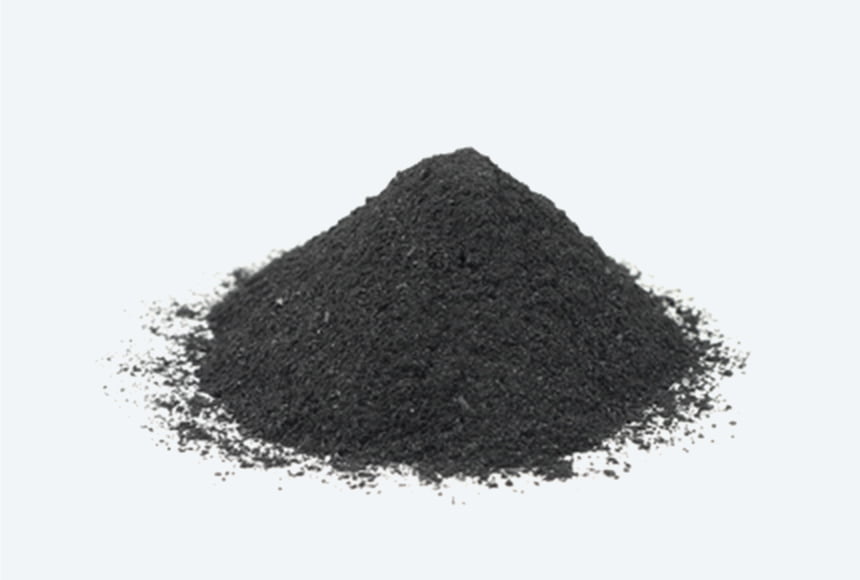
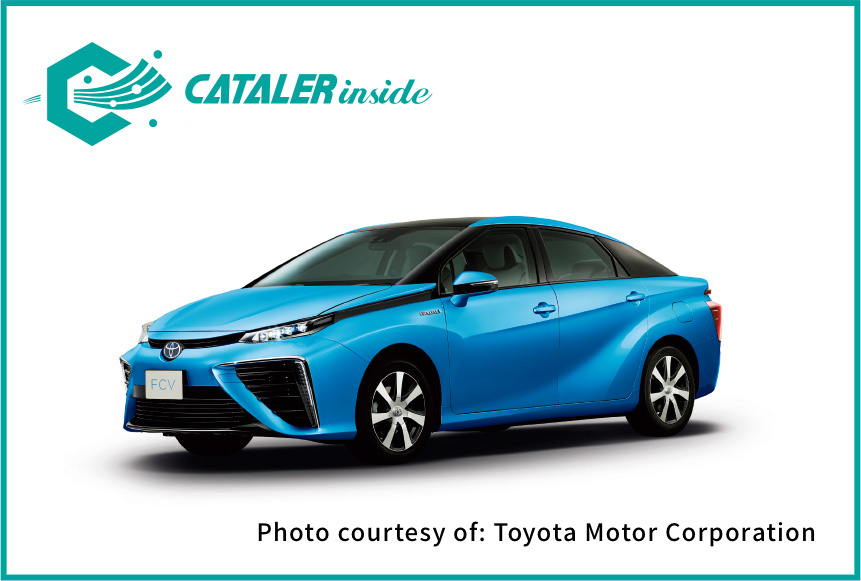
MIRAI ('14)
Carbon material for electric vehicle batteries
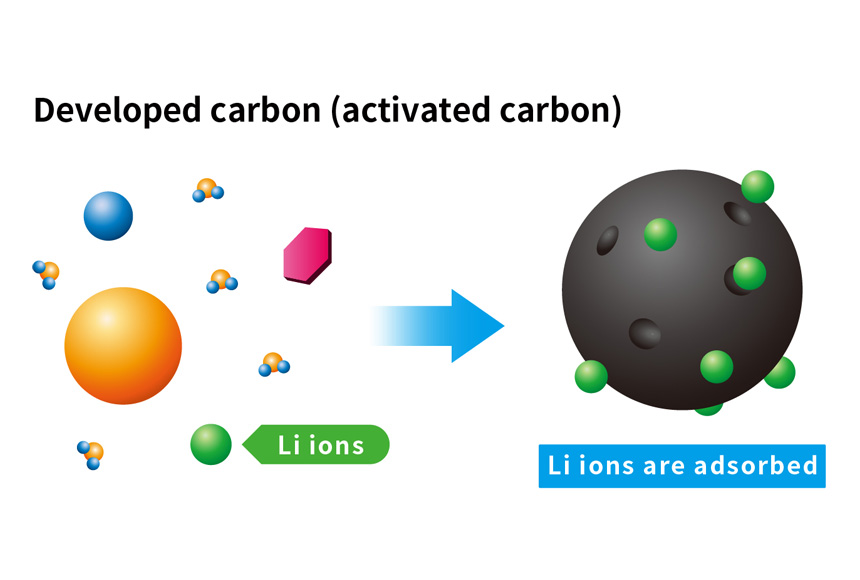
As a measure against global warming, it is extremely important to reduce carbon dioxide (CO2) emitted by automobiles. In that respect, the CO2 emissions of hybrid Electric vehicles (HEV, PHEV), fuel cell electric vehicles (FCEV), and electric vehicles (BEV) can be reduced to about 1/2 to 1/4 those of gasoline vehicles. In particular, PHEVs and BEVs are expected to be able to significantly reduce CO2 emissions from power generation to driving automobiles because they can use electric power from renewable energy sources. For more widespread use of PHEVs and BEVs, it is necessary to improve battery performance (especially to extend the mileage). Cataler has been developing carbon materials, which are constituent materials of lithium-ion batteries and functional materials for storing electricity. As a result, we developed a technology to expand and control the spaces (pores) at nanometer sizes.
It is possible to store a large amount of electricity.
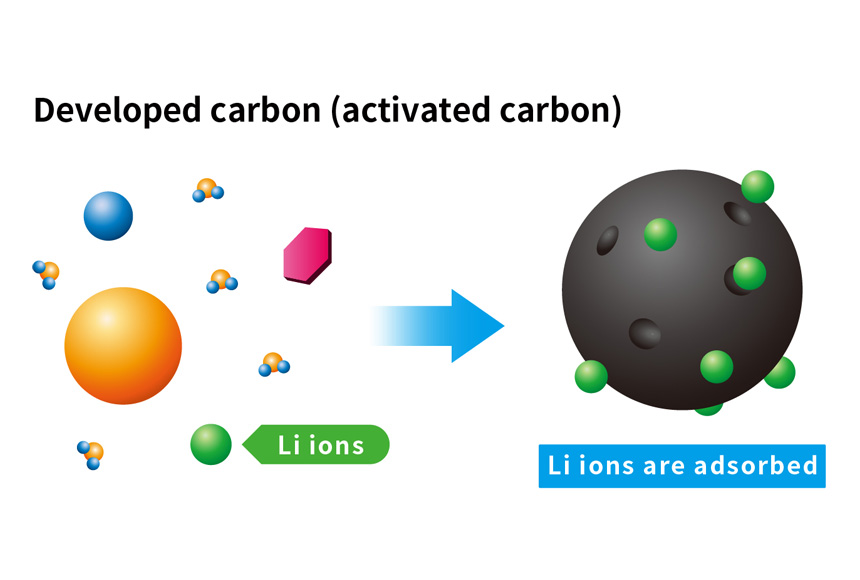
HC-SCR (hydrocarbon selective catalytic reduction) catalyst
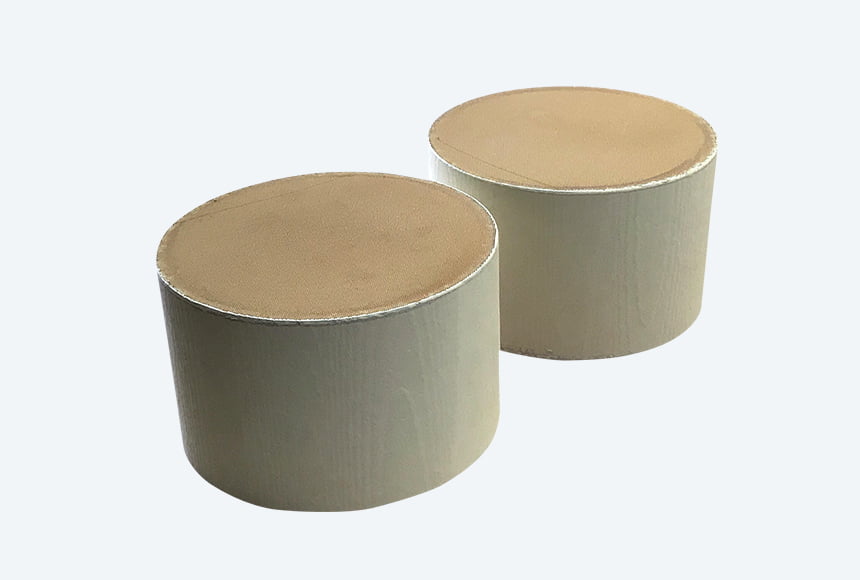
As nitrogen oxide (NOx) regulations are severe, urea SCR(*), which purifies NOx by using urea as a reducing agent, is becoming the main exhaust system. This system has problems of forcing the driver to replenish urea, and limiting its practical installation due to the need for devices such as urea tanks. HC-SCR system is very benefit because of it uses fuel for Nox reduction. By using precious metals, copper (Cu) and silver (Ag), for the catalyst, Cataler succeeded in developing the world's first catalyst with high durability and excellent NOx purification performance.
Urea SCR
Urea SCR is an exhaust gas purification technology that purifies nitrogen oxides (NOx) in the exhaust gas of diesel engines. It is same as Nox deduction by Nh3, which is used at fixed emission facility. This is an old technology patented in 1957 that uses hydrogen in ammonia molecules (NH3). O2 splited from NOx convert to nitogen(N2) and water(H2O) by catalytic reaction.
Awards
- 2018
-
- Nikkan Kogyo Shinbun / MONOZUKURI Nippon Conference "Super Manufacturing Parts Award"
- Catalyst Manufacturers Association of Japan "Technology Award"
- Hino Motors "Technology Development Excellence Award"
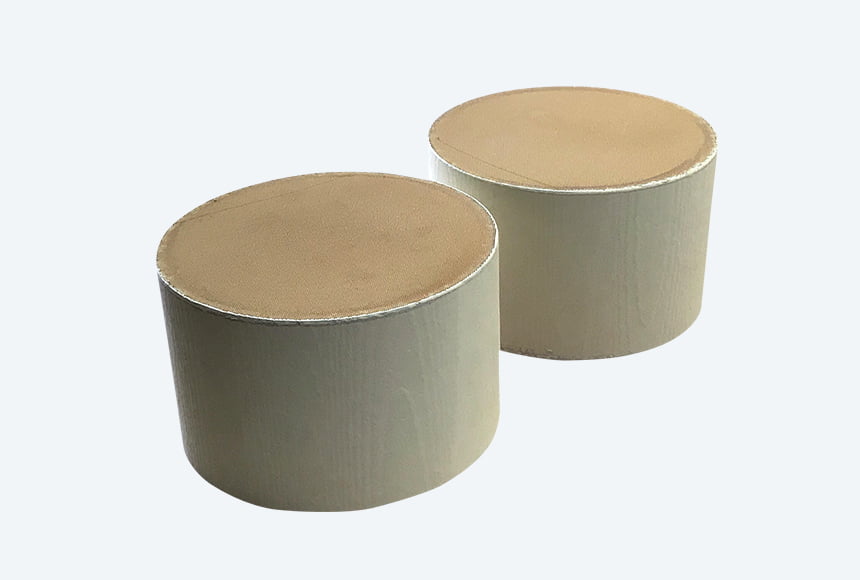
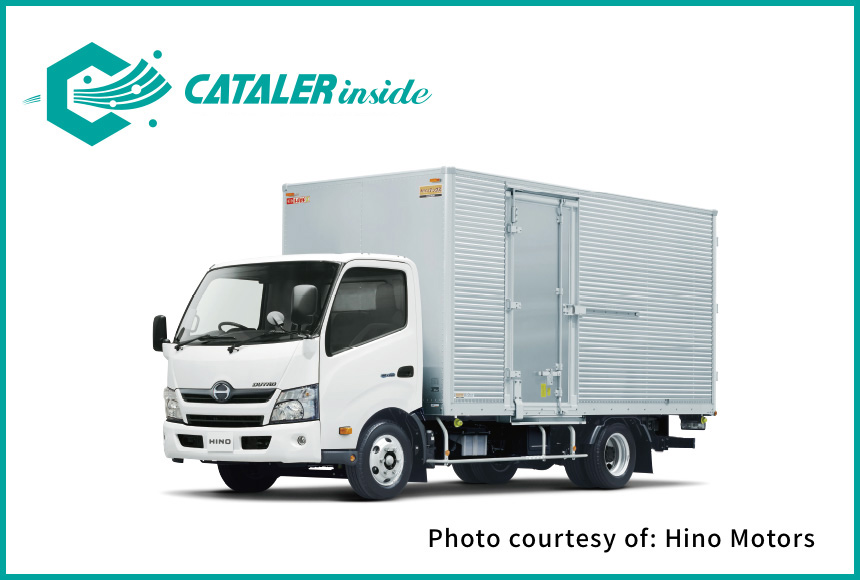
Dutro ('11)
Zone-coated catalyst
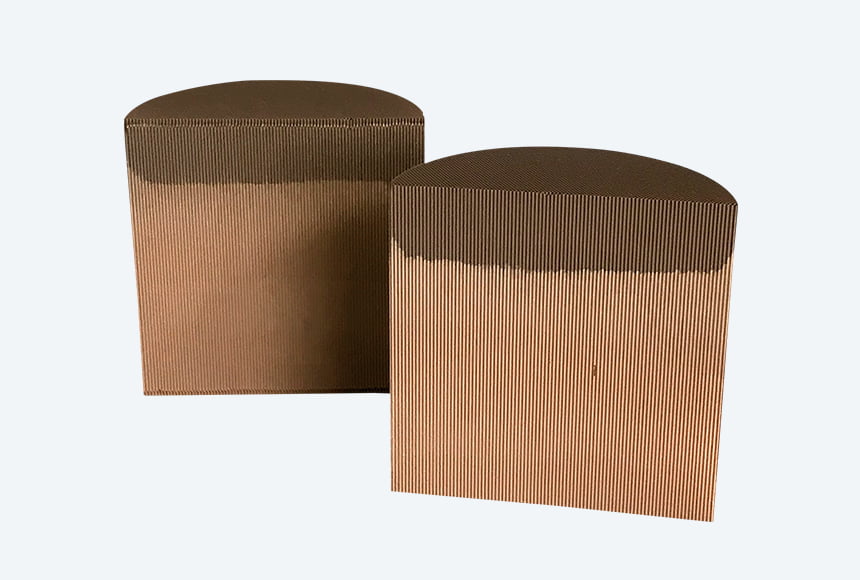
With the tightening of exhaust gas regulations around the world and the increase in the number of automobiles sold, it has become important to avoid procurement risks of precious metals and rare earths, which are indispensable components for exhaust gas purification catalysts. We reserched exhaust gas behavior in the catalyst,so we developed separating function technology follow the gas flow. The front side is hydrocarbon(HC) reduction by palladium(Pd) and the rear side is nitrogenoxiside(Nox) reduction by rodium(Rh). At the same time, we developed zone coating technology, and we was able to reduce the amount of PGM and rare earths materials. Now we optimized the zone composition of catalyst for each vihicles and this zone coating technology is our standard.
Awards
- 2012
-
- Society of Automotive Engineers of Japan, Inc., "Technical Development Award"
- Toyota Motor "Technology & Development Award"
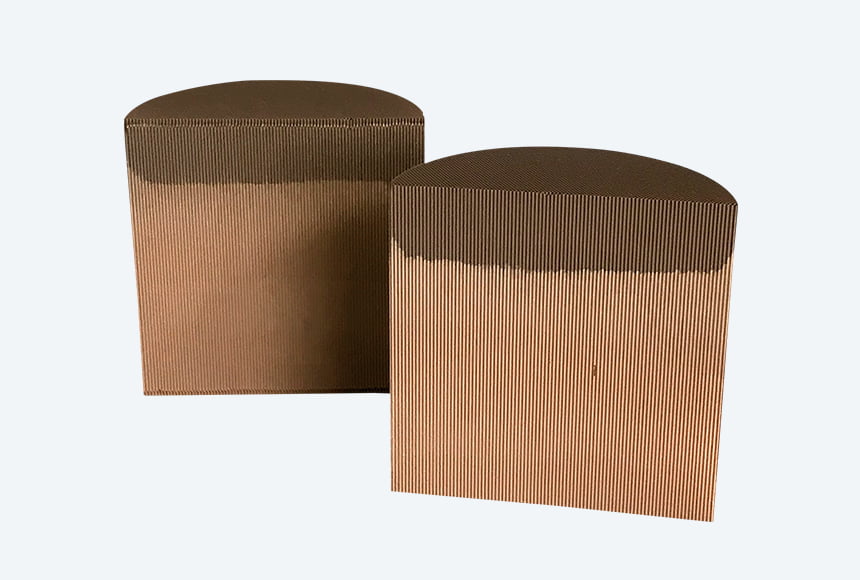
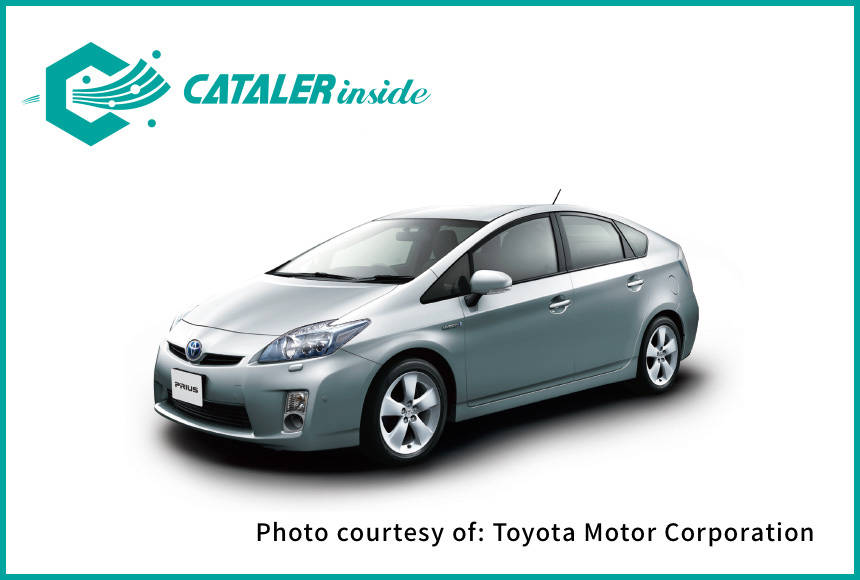
Prius ('09)
Key technologies
GPF catalyst
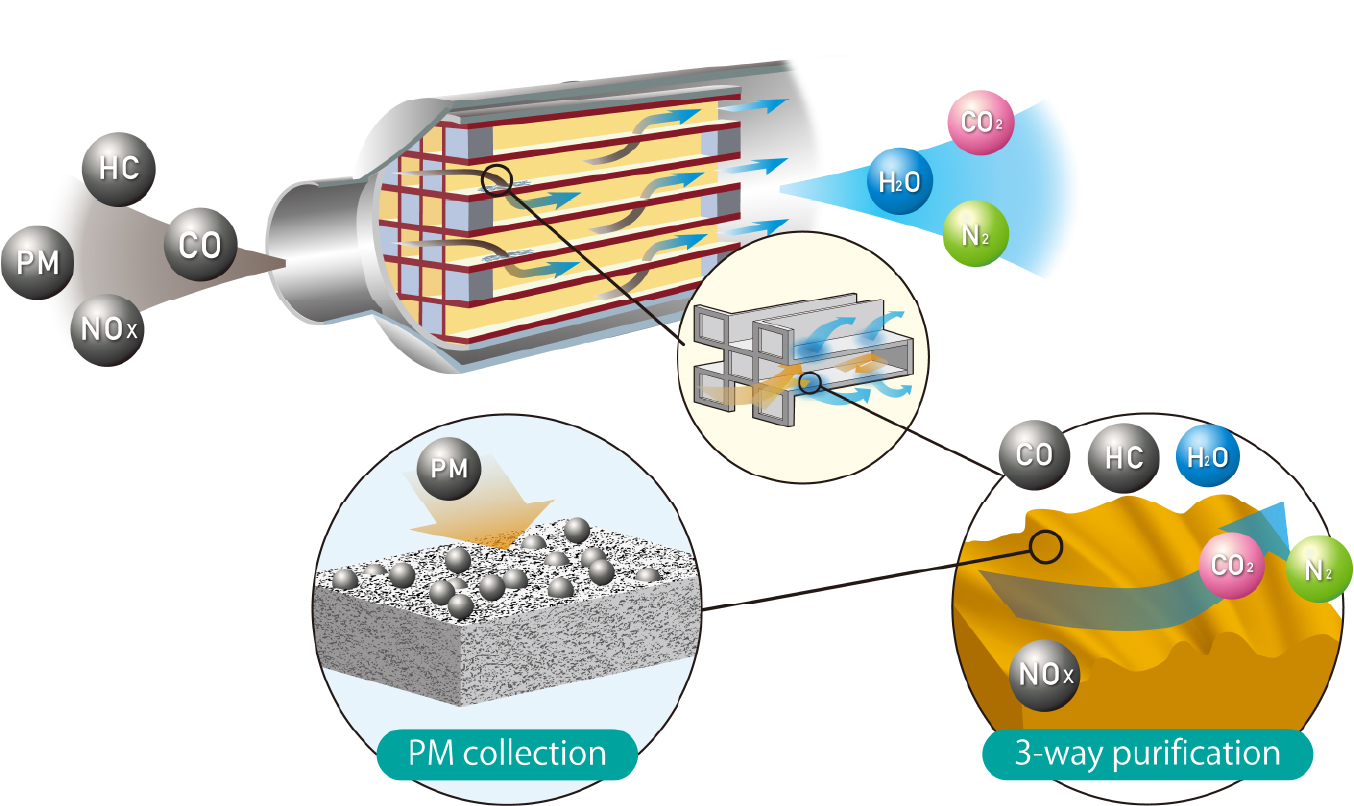
GPF catalyst
The particulate matter emission regulated for not only diesel vehicles also gasoline vehicles. We developed 4-way catalyst which trap the PM in order to clear the PM regulation by 3-way materials coating on the filter substrate.
Awards
- 2019
- Toyota Motor "Technology & Development Award"
New oxygen storage material (pCP)
Conventional material
New oxygen storage material (pCP)
New oxygen storage material (pCP)
One of the technologies required to comply with various countries' emission regulations is technology to reduce nitrogen oxide (NOx) emissions. We researched "NOx behavior" in the oxygen swing condition, and we developed "new oxygen storage material"(PCP) which is wide range activity in the oxygen swing condition.
2000sdevelopment history
Intelligent catalyst
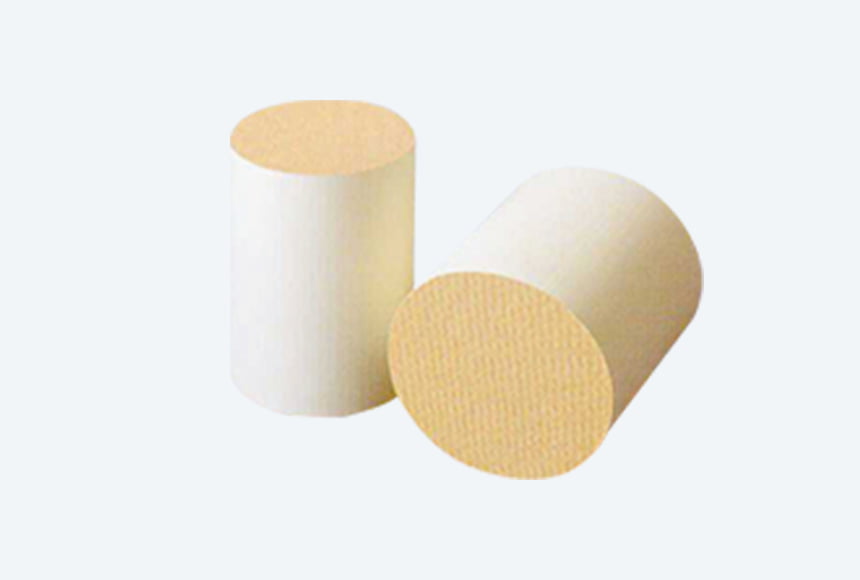
We developed intelligent catalyst with Daihatsu Motor Co.,LTD which use new technology that Platinum Group Metals is included in the perovskite oxide. The intelligent catalyst functions acording to exhaust gas condition change by the nano size Platinum Group Metals particles in the rich condition. The intelligent catalyst functions acording to exhaust gas condition change by the nano size Platinum Group Metals particles in the rich condition. In the lean condition, intelligent catalyst become stable perovskite oxide again. We can consisted the high catalyst activity and very low Platinum Group Metals amount because of this Platinum Group Metals self-regeneration.
Perovskite oxide
In ABO3 type oxide, of the cation A is same size as oxygen anion, the solid can become perovskite structure. The cation A and oxigen anion become close-packed hexagonal lattice in the perovskite structure. The cation B occupys 6 coordination site around only oxigen anions. The perovskite structure varies flexible. It can be unspecified compound through oxygen lack and layer structure,which is very convenient for designing materials having various functional properties. Therefore, we expect the progress investigation of perovskite structure and phisicallity.
Source: Bulletin of the Japan Institute of Metals, Vol.26, No.8 (1987) 771
Awards
- 2004
-
- Catalysis Society of Japan "Society Award" (Supervisor Norio Kimura)
- Toyota Motor "Technology Excellence Award"
- Daihatsu Motor "Technology Excellence Award"
- 2003
-
- Catalyst Manufacturers Association of Japan "Technology Award"
- Society of Automotive Engineers of Japan, Inc., "Technical Development Award"
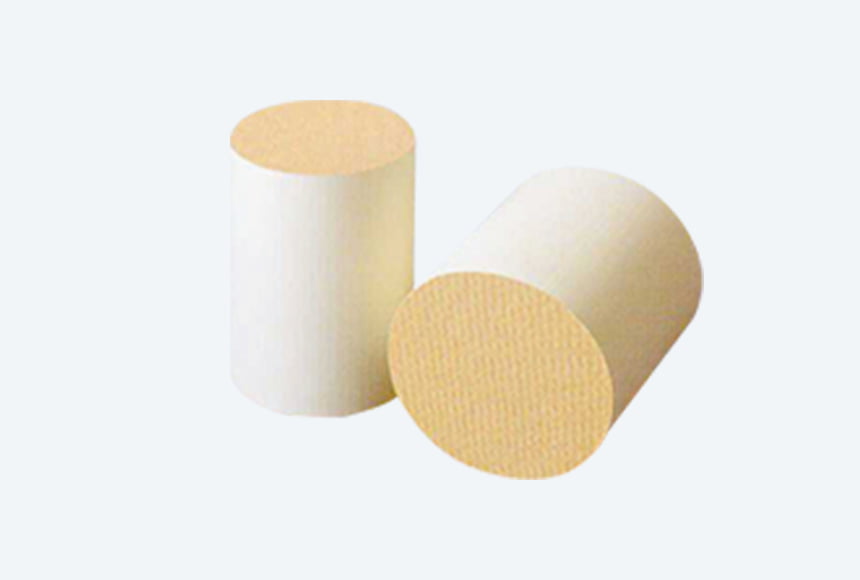
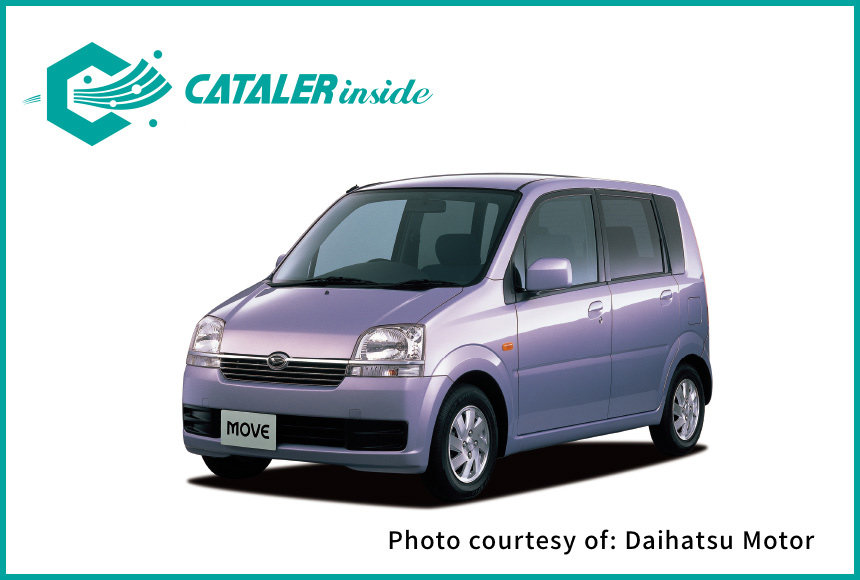
Move ('02)
DPNR catalyst
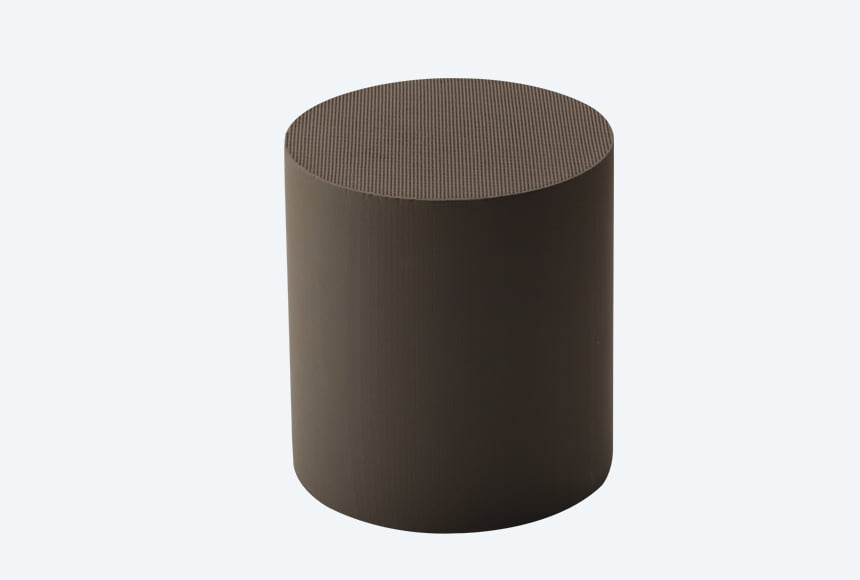
In 2003, we developed DPNR (Diesel Particulate and NOx Reduction system) technology, which combines Diesel Particulate Filter (DPF) technology with a NOx (nitrogen oxide) storage reduction catalyst, and were the first in the world to successfully put it into mass production. We can coating the Nox strage materials inside the DPF substrate wall, enabling two exhaust purification actions on particulate matter (Particulate Matter / PM) (*) and NOx with one catalyst. It makes to be small and light and low cost aftertreatment system. We developed low pressure drop DPNR catalyst by our original filter coating technology. This coating technology drives to improve engene performance. And, the fuel addition from the exhaust port injector enables the PM regeneration and Nox reduction.
Particulate Matter (PM)
A particle of solid or liquid in microns.
PM emitted from a diesel engine contains fine particles having a particle size of 10 μm or less, and floats in the air for a long time. Therefore, it is called suspended particulate matter (SPM), and is considered to be the main cause of air pollution.
Awards
- 2004
- Toyota Motor "Technology & Development Award"
- 2001
- Nikkei BP "Nikkei BP Award"
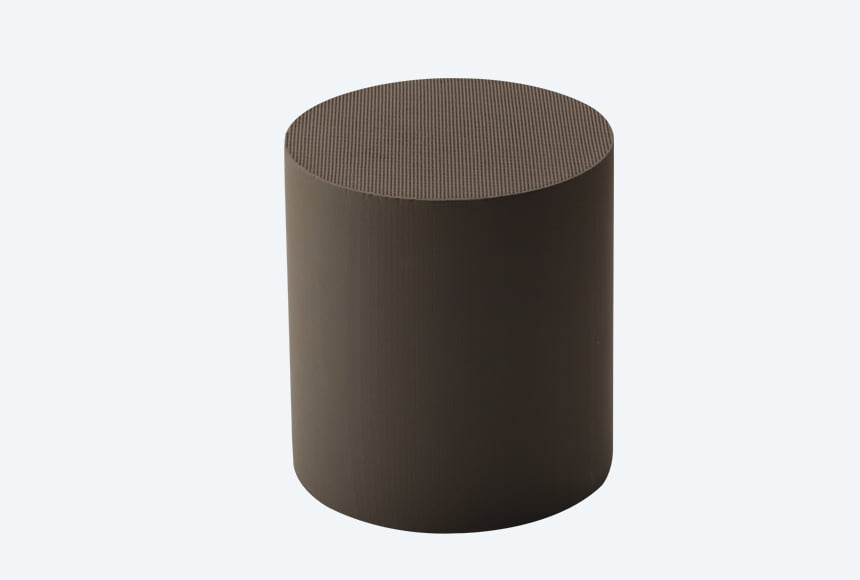
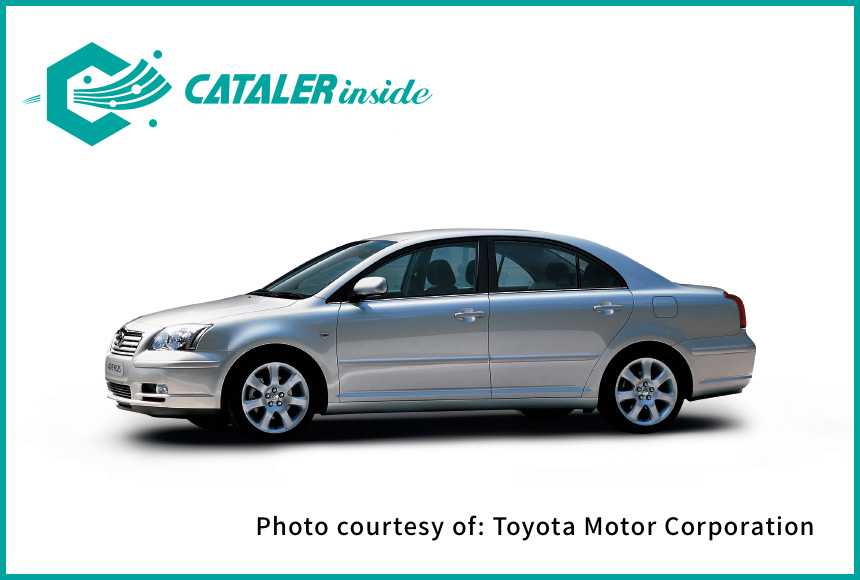
Avensis ('03)
Front highly supported catalyst
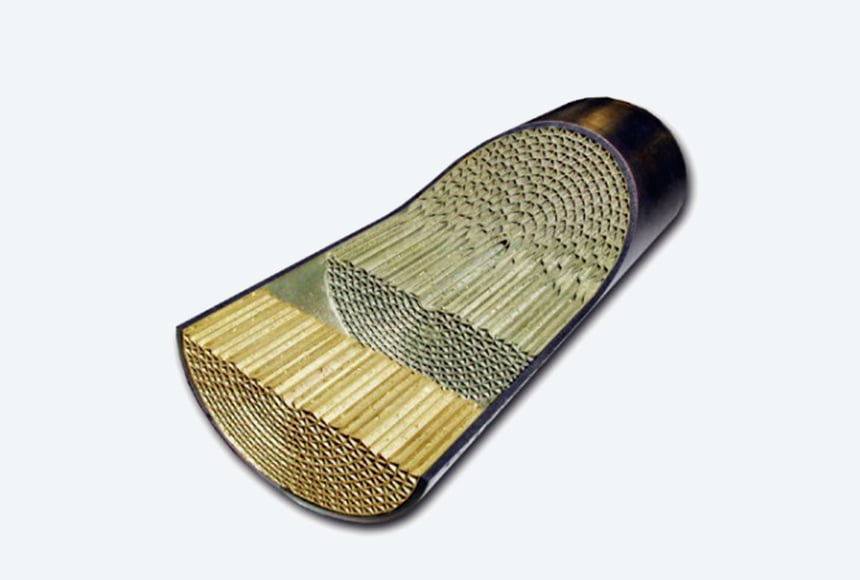
Since the EUROⅢ regulation, a cold start (*) is now required. Due to the layout of motorcycles, it is difficult to mount the catalyst directly under the engine, so it is installed inside the rear muffler. Therefore, the issue was how to increase its low temperature activity in a cold start. The front highly supported catalyst is a tandem substrate that combines a small metal honeycomb in the front stage and a main honeycomb in the rear stage, and the small honeycomb in the front stage is further supported with a high density of precious metals. In the front stage, the low temperature activity of developed catalyst is higher than our conventional catalyst because the low thermal capacity and high PGM density. And the tandem layout is high mixture of exhaust gas in the high space velocity and we ahcieved total exhaust emission reduction.
Cold start
Cold start is a mechanical term that primarily refers to starting a thermal engine (engine) or an electric motor when it is as cold as or colder than the ambient temperature of the environment in which it is located.
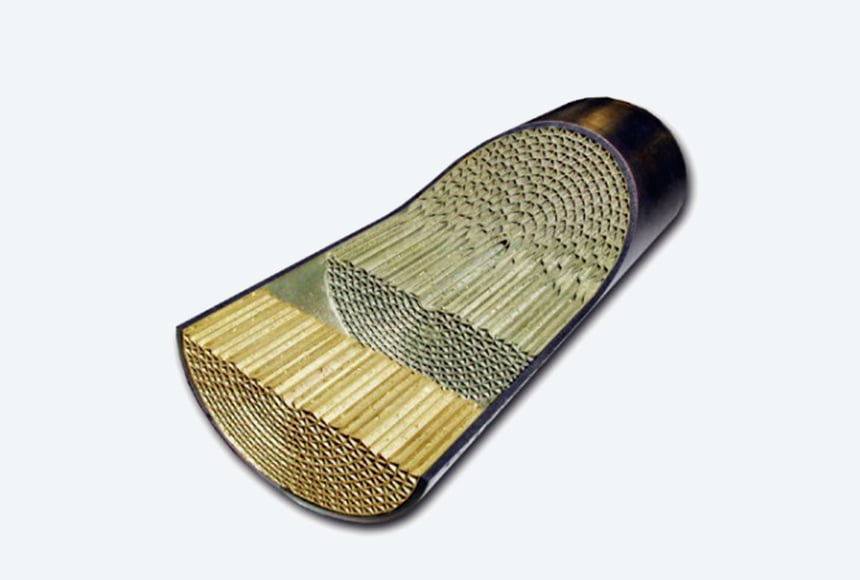
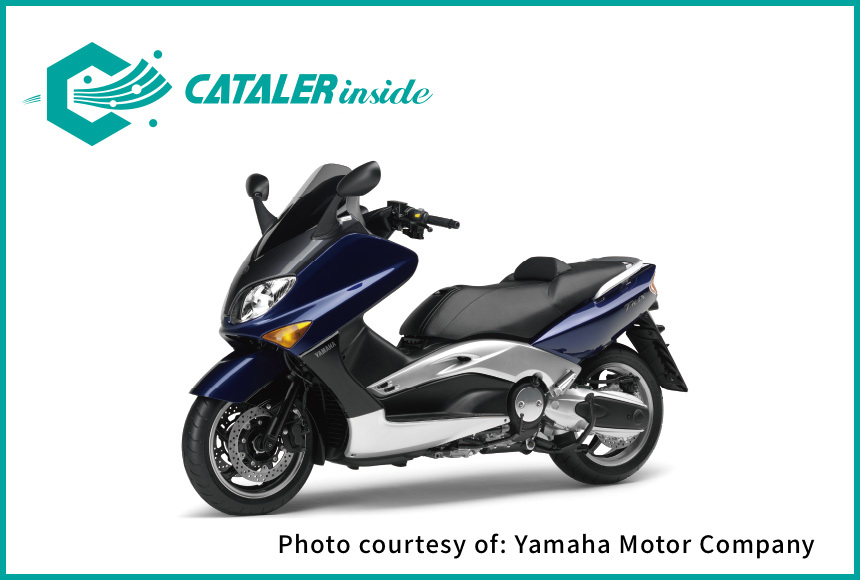
TMAX ('06)
Key technologies
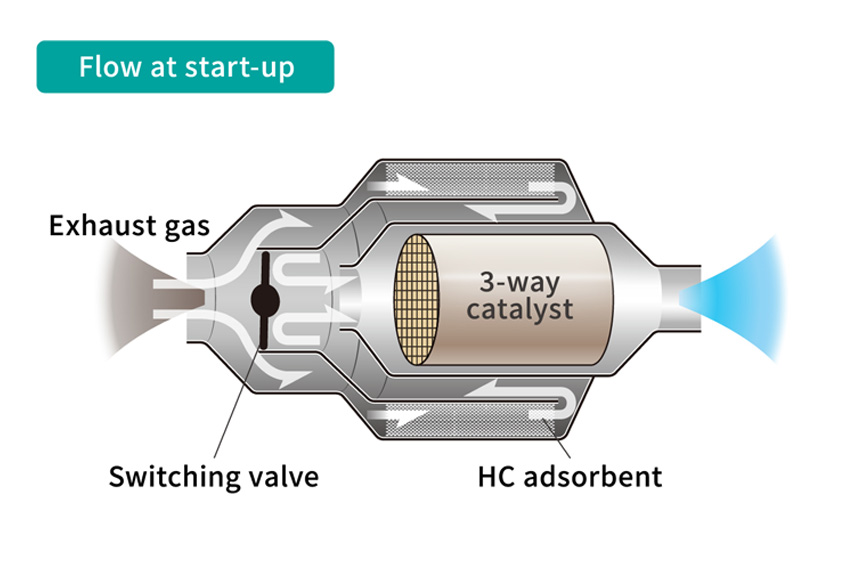
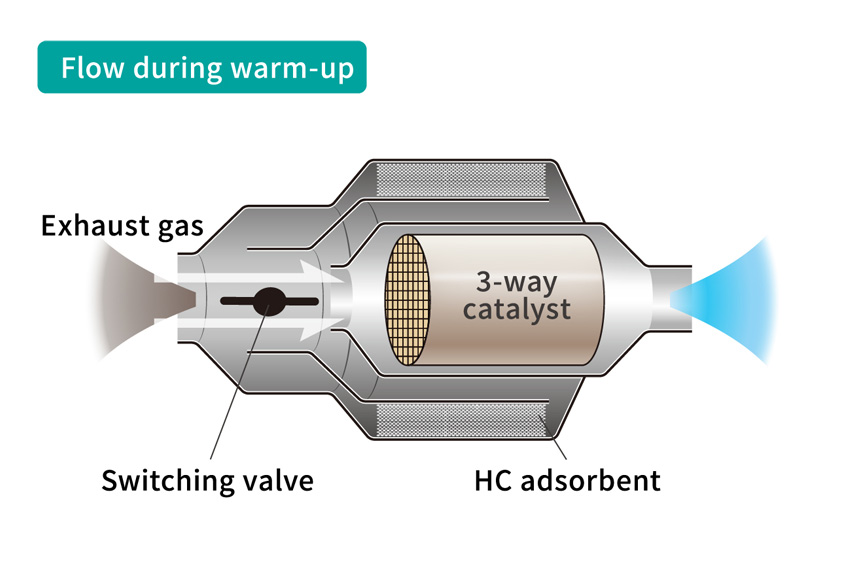
Coaxial type HC adsorption cylinder for US SULEV (*)
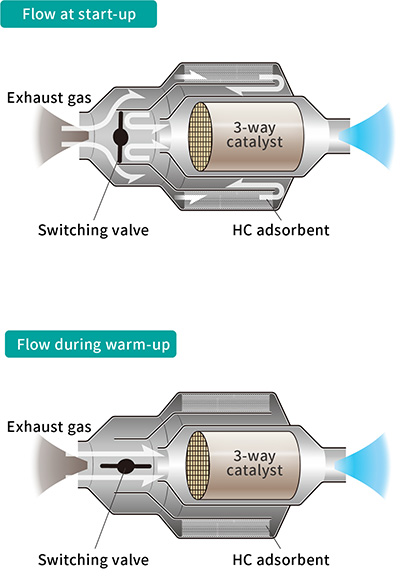
This technology aims to reduce hydrocarbon (HC) emissions at low temperatures. Immediately after starting the engine, HC is temporarily trapped by the donut-shaped HC adsorption layer on the outside of the catalyst. The HC adsorbed on catalyst layer desorbs along the temperature rising, and The catalyst purifies adsorbed HC. This HC adsorption vessel like a donut can be very low HC emission at low temperature, making it possible to comply with SULEV regulations in California, USA.
SULEV (Super Ultra Low Emission Vehicle)
"Super Ultra-Low Emission Vehicle" in the US.
SULEV is a vehicle that is subject to the emission regulations of the California Air Resources Board, which are considered to be the most stringent in the world, and whose emissions of harmful substances such as nitrogen oxides (NOx) and non-methane hydrocarbons (NMHC) are even lower than the standard values for Ultra Low Emission Vehicles (ULEVs). Extremely low pollution vehicle. Ultra-low emission vehicle.
[Supplement] In Japan, this is the case for automobiles that have reduced harmful substances by 75% or more from 2005 emission regulation standard values.
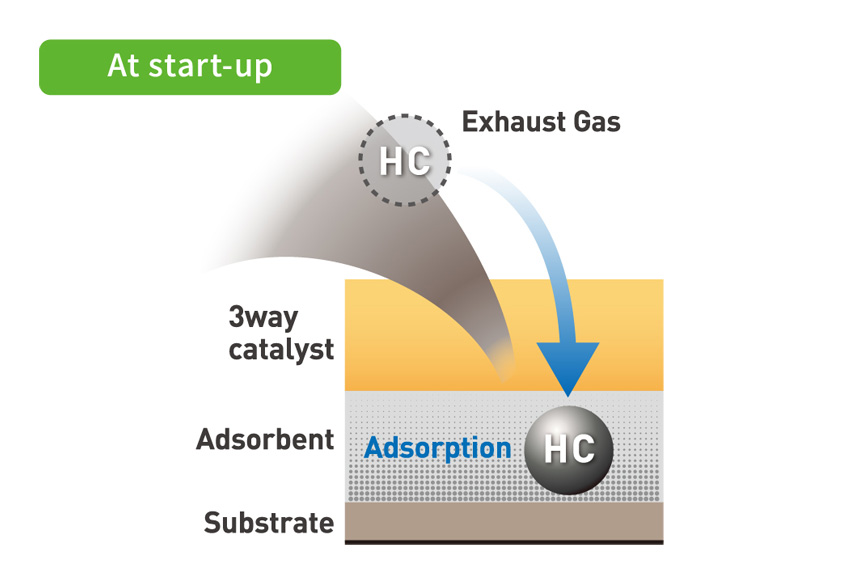
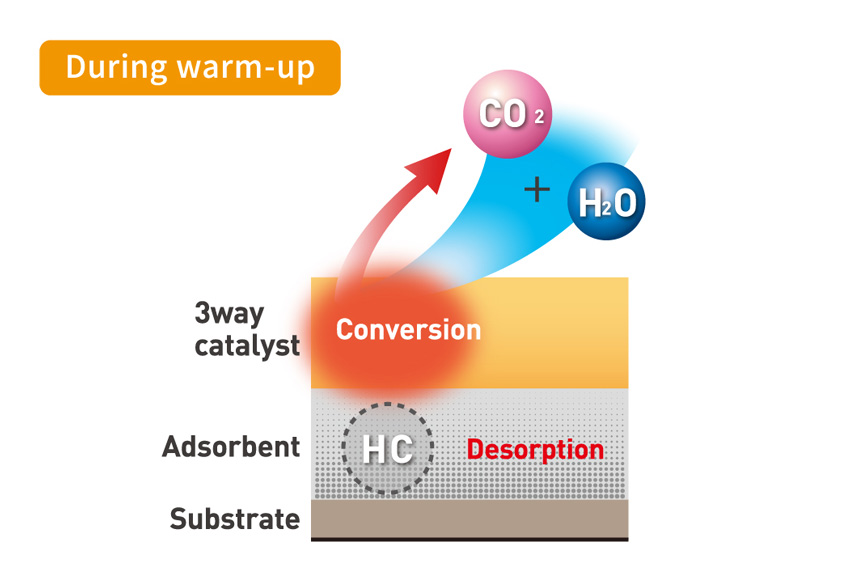
HC adsorption-purification type 3-way catalyst
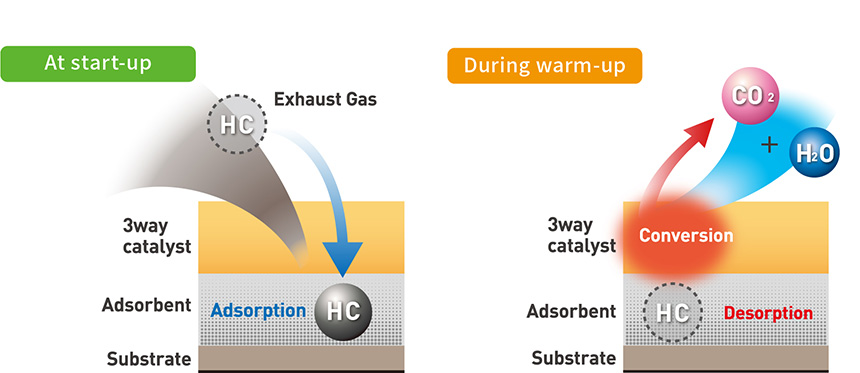
In order to clear the P-ZEV (*) regulations of California, USA, an adsorption layer and a catalyst layer are placed in one catalyst. The HC is adsorbed by adsorption layer and it is desorbed at the range of high catalyst active temperature. Therefor we can reduce harmful substances(cold emissions) from the starting up engine.
P-ZEV (Partial Zero Emission Vehicle)
In the sense of "partially zero emission vehicle" in the United States, this vehicle is certified as one that has cleared the strict standard for gas emissions, although it is not as good as an electric vehicle (BEV) or a fuel cell electric vehicle (FCEV).
Since 2003, it has been obligatory to sell a certain proportion of "vehicles with zero airborne particle emissions" promoted by the California government ", and some ULEVs (ultra-low emission vehicles) and hybrid electric vehicles (HEVs) correspond to this.
1990sdevelopment history
NSR (Nitrogen Oxide Storage-Reduction) Catalyst
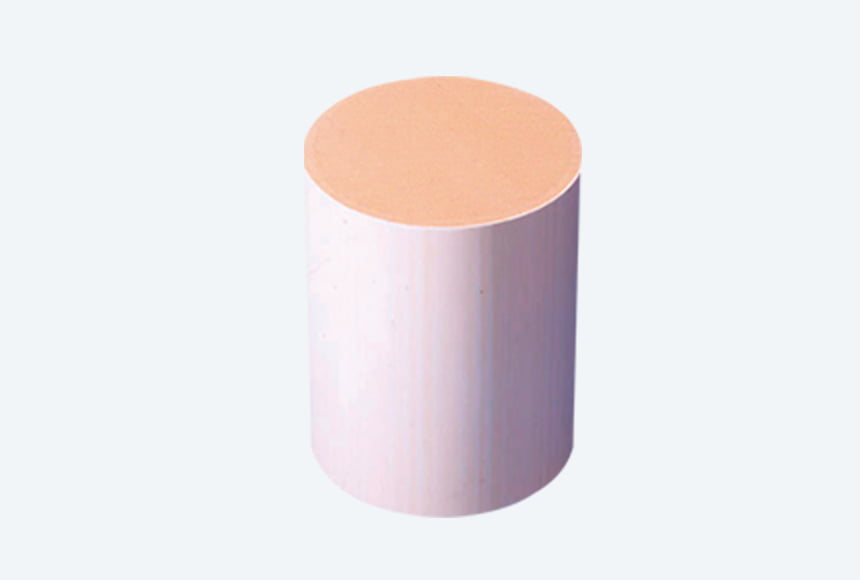
The NSR(Nox storage reduction) catalyst is the efficient Nox reduction technology that in the exhaust gas from lean combustion. It can result high fuel efficiency and clean exhaust gas.
In the NSR catalyst, Nox from lean burn is oxidized on the PGM and storaged as nitrate on the strage materials like barium (Ba) of the NSR catalyst temporary.
Then the Nox is reduced to N2 by the reductive during short rich burn(rich spike). And, by loading NOx strage materials such as Ba and potassium (K) and precious metals in a highly dispersed state and in close proximity, we achieved high NOx purification performance in the lean region. We were able to supply the lean burn vbhicle for the first commertial production in the world.
Awards
- 1995
-
- The Chemical Society of Japan "Chemical Technology Award"
- Society of Automotive Engineers of Japan, Inc. "Technical Development Award"
- Toyota Motor "Technology & Development Award"
-
- The Japan Society of Mechanical Engineers "Technology Award" (System)
- Japan Society for the Promotion of Machine Industry, "Chairman's Award" (System)
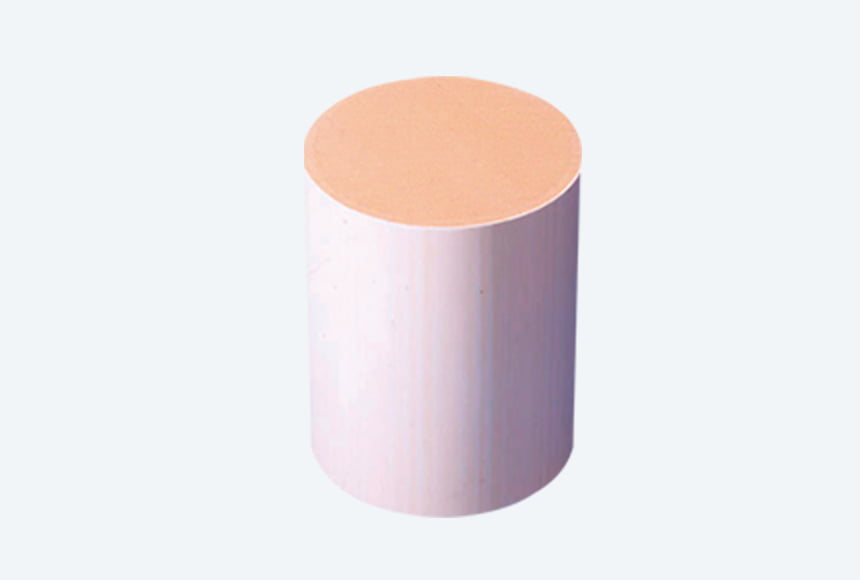
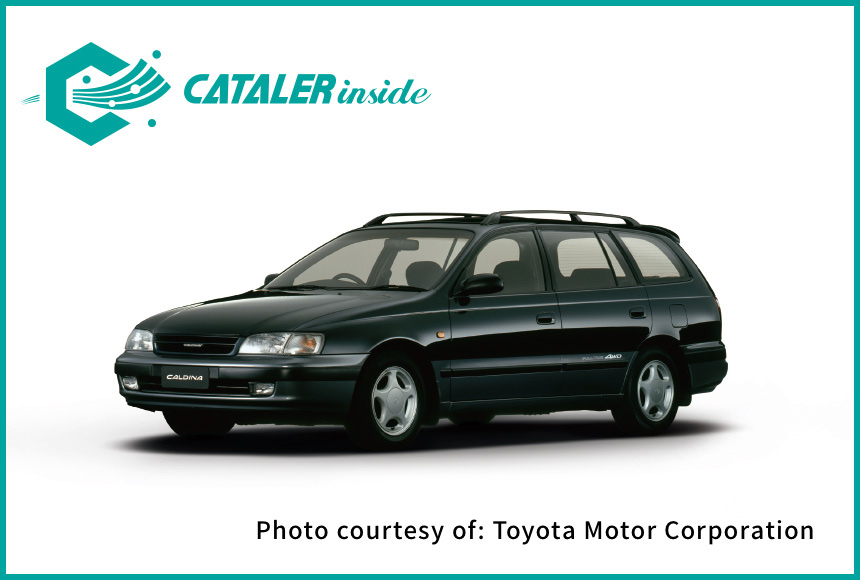
Caldina (Lean Burn) ('94)
Pd-only 3-way catalyst
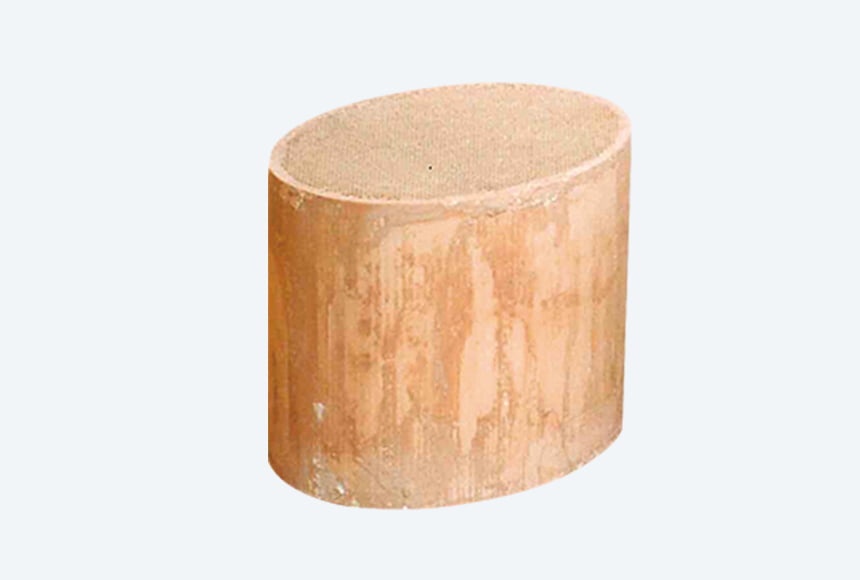
Due to the soaring market price of rhodium (Rh) of 30,000 yen/g or more, we started the development of a 3-way catalyst using only palladium (Pd), which was inexpensive at that time. It was known that Pd alone exhibited ternary properties, but heat resistance and poison resistance were issues. We improved the thermal stability of the main matelial, alumina, and discovering the effect of barium (Ba) in mitigating Pd poisoning, we were able to find a solution and realized mass production of the first Pd-only three-way catalyst in Japan. The knowledge gained at this time led to our first presentation at SAE (Society of Automotive Engineers) (*).
SAE(Society of Automotive Engineers, Inc.)
American Society of Automotive Engineers. A non-profit organization in the United States whose members are mobility professionals. They develop standards related to automobiles and aerospace, hold expert meetings, publish books and magazines on power equipment, and engage in educational activities to promote the development of mathematics, science and engineering. Members are individuals such as engineers, corporate officers, educators and students. The US automotive industry is central to its activities, with approximately 90,000 members from nearly 100 countries around the world.
Awards
- 1994
-
- Catalysis Society of Japan "Technology Award"
- 1993
-
- Toyota Motor "Cost Excellence Performance Award"
- Yamaha Motor "Cost Reduction Performance Award"
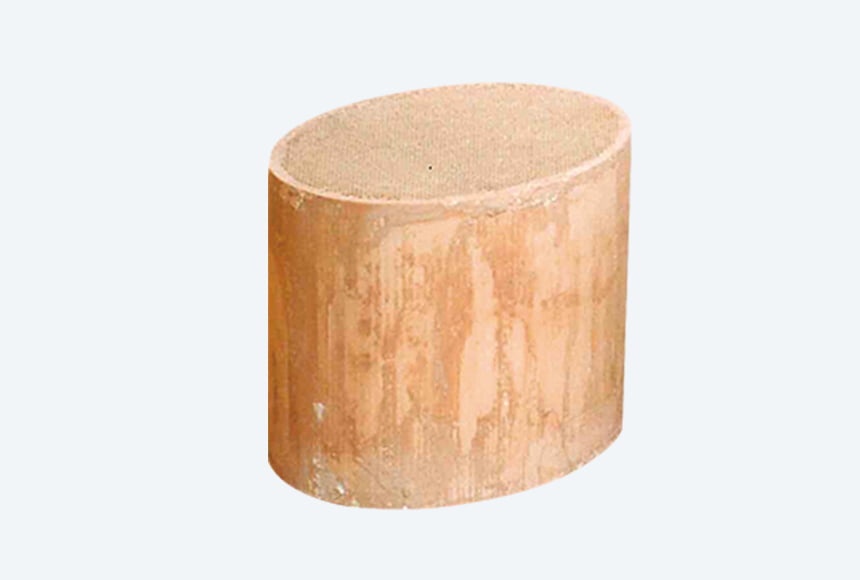
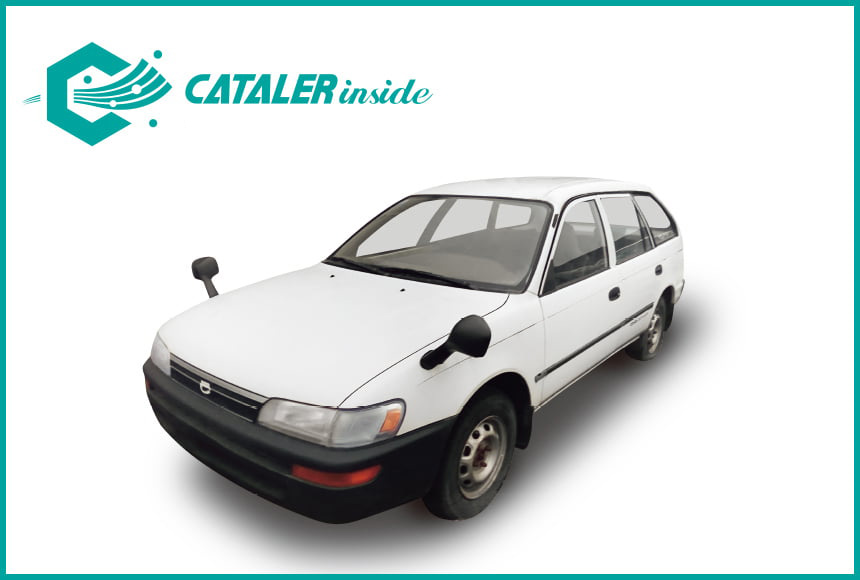
Corolla Van ('90)
Key technologies
Diesel oxidation catalyst
We succeeded to develop the sulfer resistant materials for escaping catalyst deactivity by high sulfer fuel using before our competitors. It has also become possible to comply with stricter regulations by adopting zeolite, which is a hydrocarbon adsorbent.
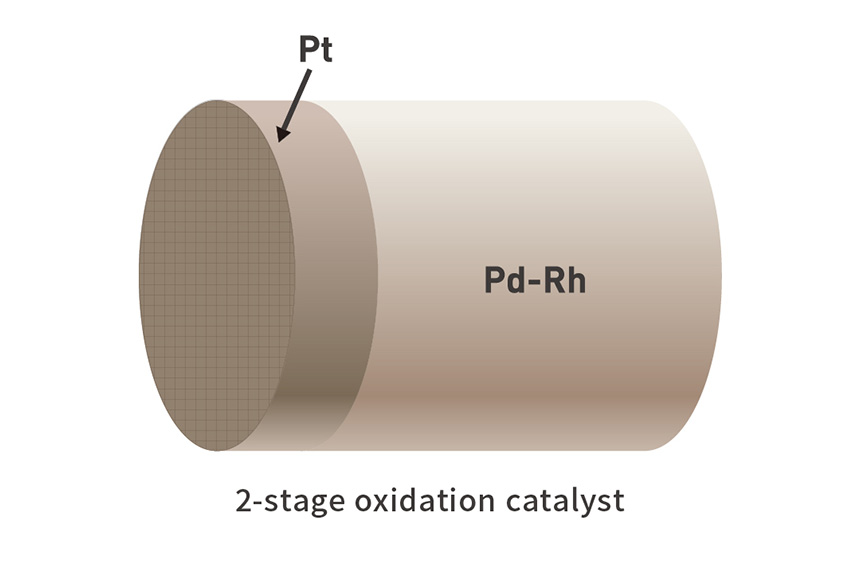
Hexagonal cell catalyst
The thickness of catalyst layer is different the corner and flat position on the conventional square substrate. Therefore, We developed the coating method optimized for the hexagonal substrate,and by making uniform catalyst layer.
The catalyst activity was very higher by utilizing PGM function effectivity.
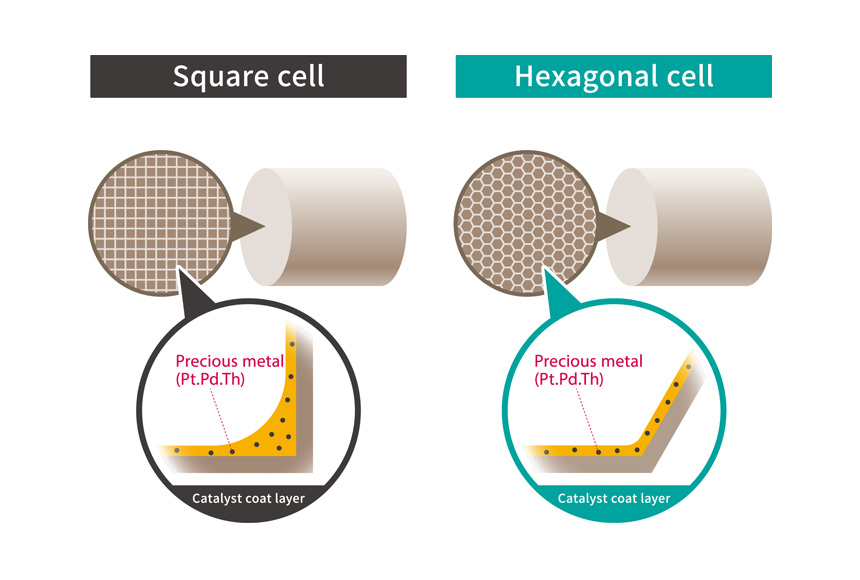
1980sdevelopment history
Approaches to 2-wheel 2-stroke emissions
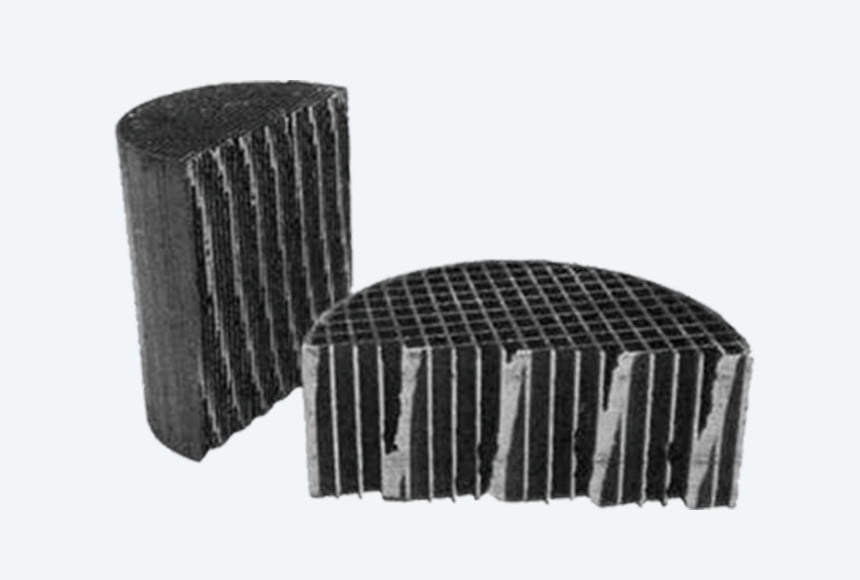
At that time, the demand for high out put, compact and lightweight 2-stroke engines was increasing for motorcycles, which required different emission control measures from those for 4-wheel vehicles. Two-stroke engines produce a large amount of unburnt gas, and conventional monolith catalysts have a problem with hydrocarbon (HC) combustion causing melting down. As a solution to this problem, a 2-stage reactive catalyst is used, where HC is partially combusted in low density cells in the first stage (engine side base material) and a monolithic catalyst with high density cells is used in the second stage (muffler side base material). In 1983, a Cataler catalyst was adopted for a motorcycle equipped with the world's first water-cooled, 2-stroke engine on a 50cc scooter. Then, in the 1990s, in Taiwan, where the use of motorcycles rapidly became more widespread, national emission control measures began, and the motorcycle catalyst business developed.
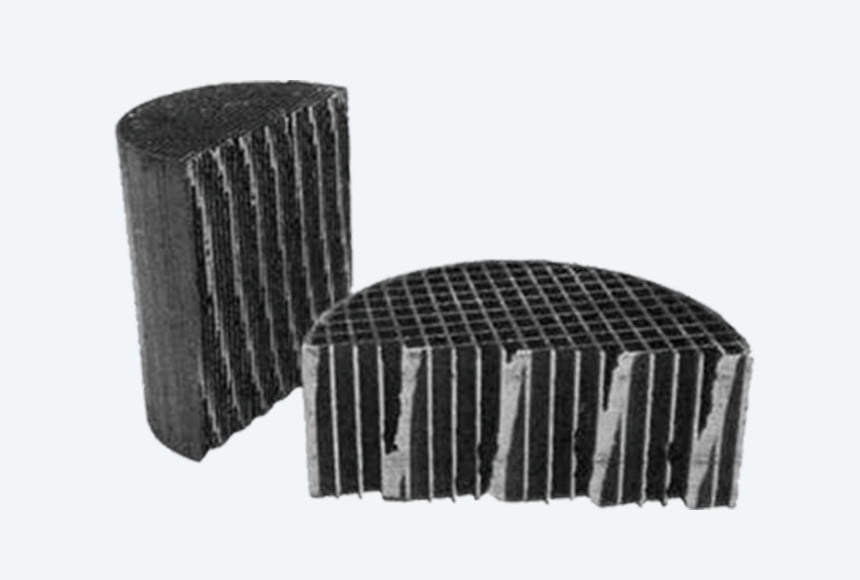
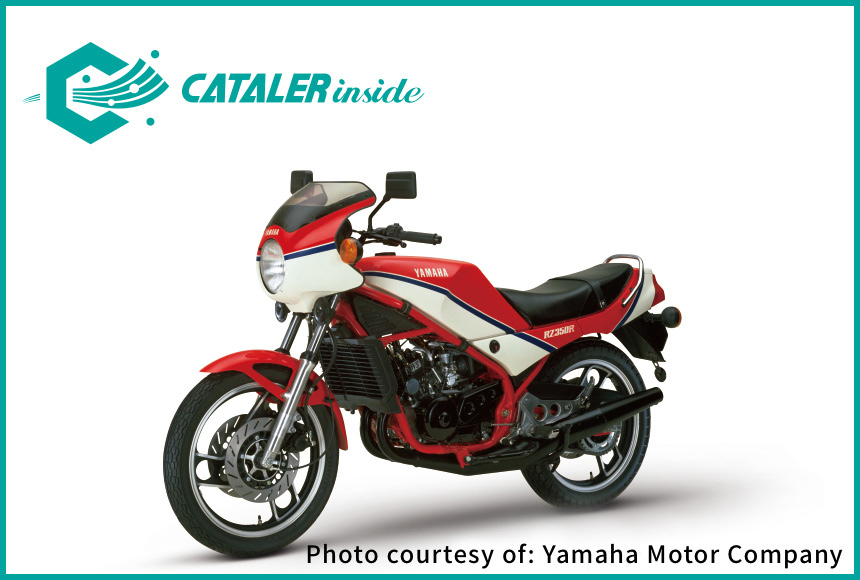
RZ350 ('83)
Key technologies
Maniverter catalysts
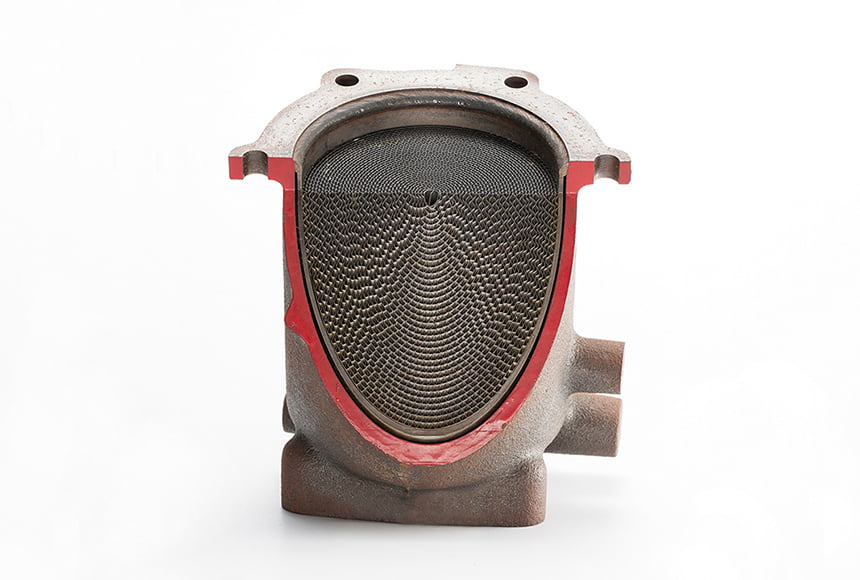
As the heat resistance of the material increased, a catalyst converter is installed directly under the exhaust manifold with the aim of early activation of the catalyst, making it possible to efficiently handle high-temperature exhaust gas.
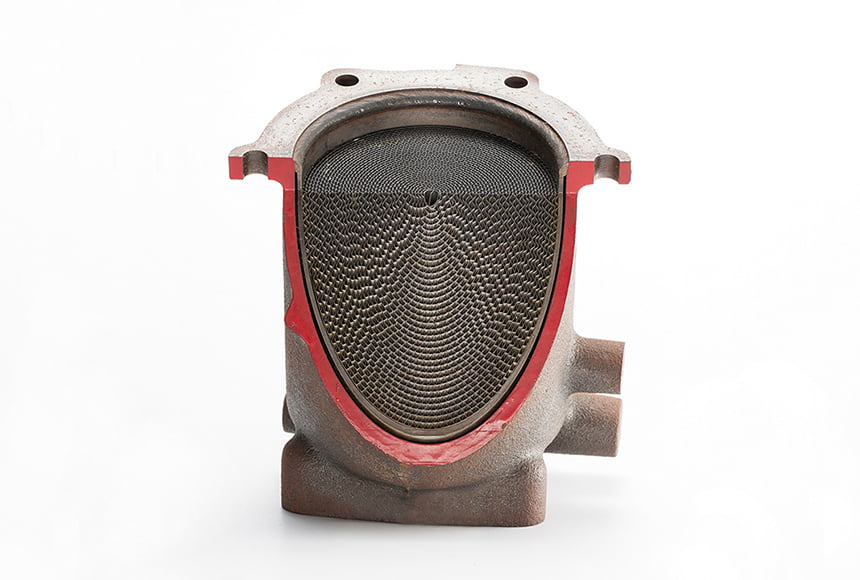
1970sdevelopment history
Pellet type exhaust gas purification catalyst
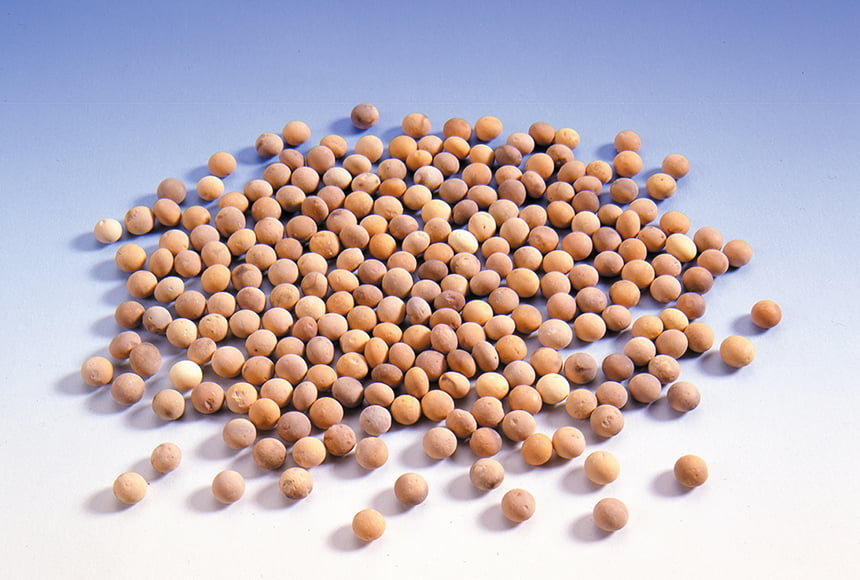
We mass-produced a palladium (Pd)-based pellet-type oxidation catalyst and a platinum (Pt)/rhodium (Rh)-based pellet 3-way catalyst that conform to emission regulations for the first time in Japan. Pellet catalysts are 2-4 mm in diameter, and consist of a very thin layer of palladium (Pd) or platinum (Pt)/rhodium (Rh) precious metals on an alumina surface. Alumina has many pores, and its surface area is 50-150㎡/g, so it is able to react harmful exhaust gases enough. The pellet catalysts, which are normally packed in stainless steel vessels with excellent heat and corrosion resistance, have been a melting down at ultra-high temperatures. But combined with precise engine control, the pellet catalysts became using wide range condition.
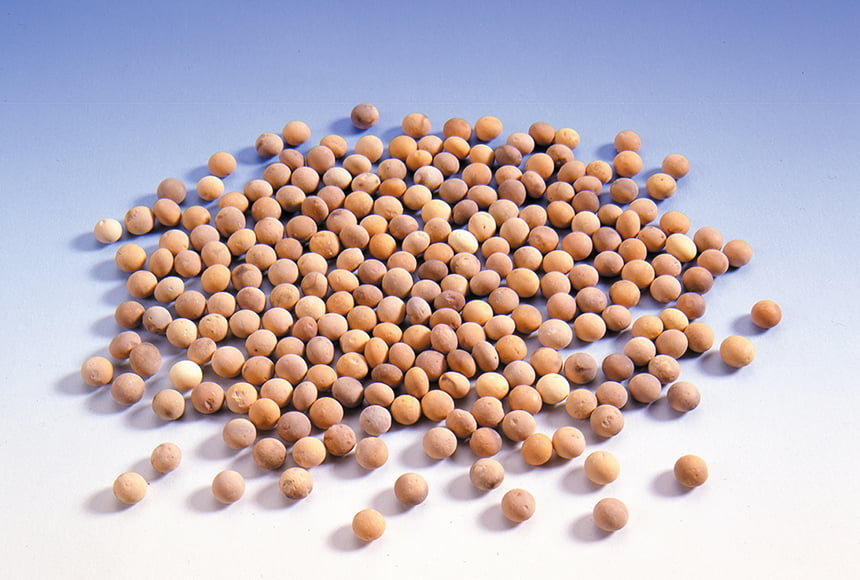
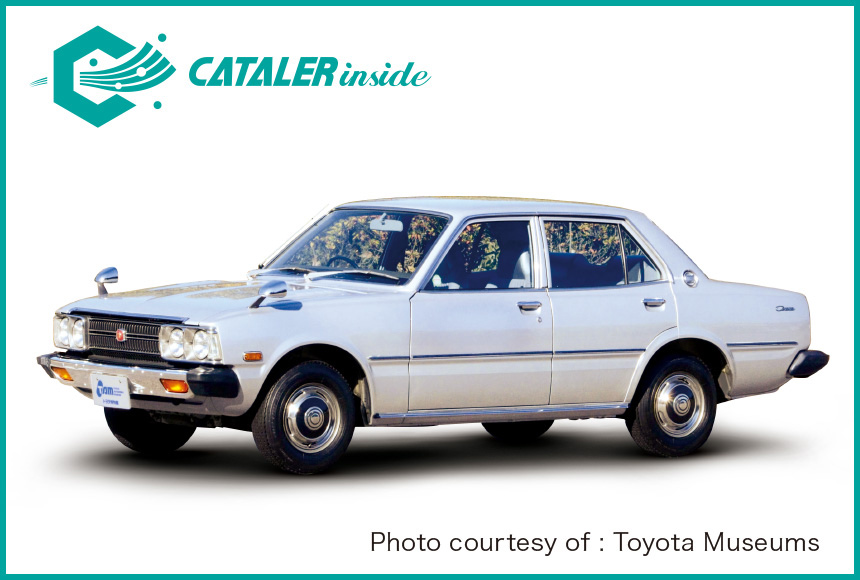
Toyopet Corona RT102 ('76)
Key technologies
High heat resistance catalyst
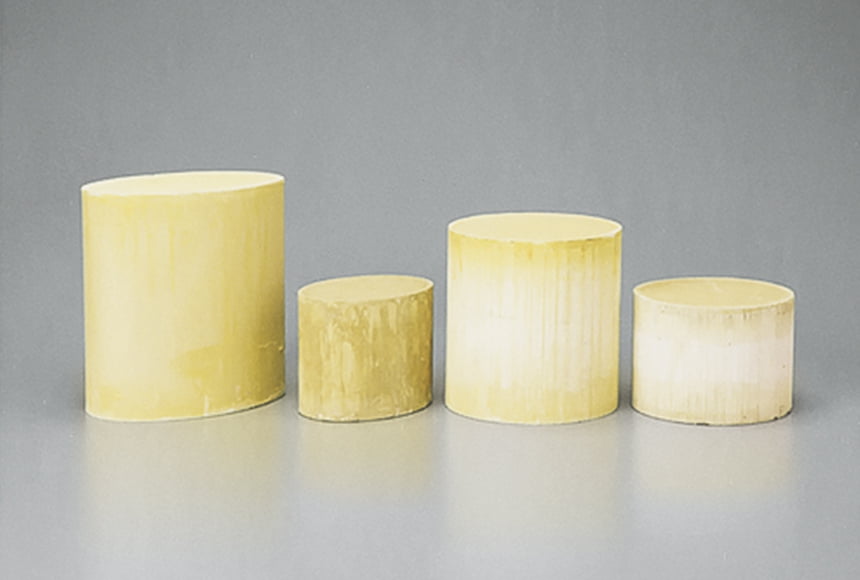
Melting of the honeycomb was more of a problem than the effect of heat on the alumina pellets, and measures against increase of pressure loss were an issue. By linking with the engine control system, it is now possible to use honeycombs by suppressing the temperature rise of the catalyst layer.
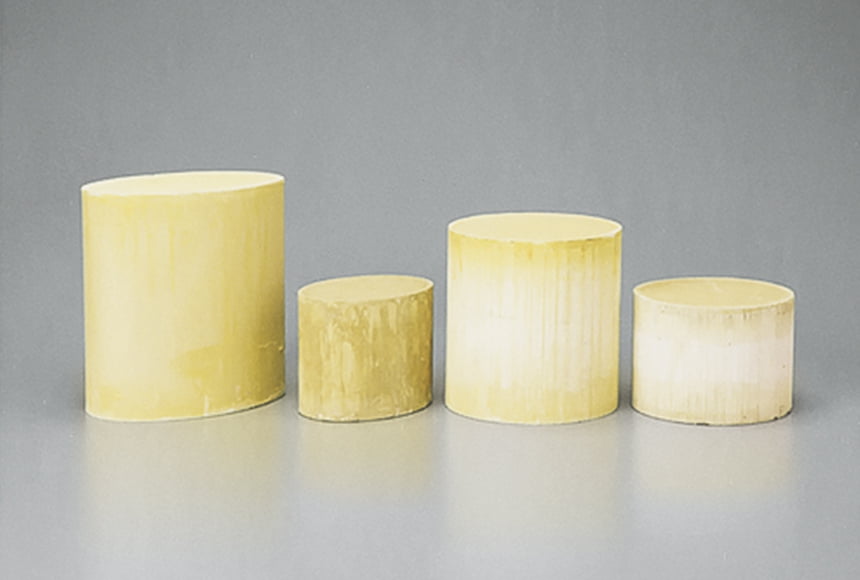