- Home
- Unique Activities
- Work quality improvement activities
Work quality improvement activities
Cataler strengthens various corporate activities using Total Quality Management (TQM). One of them is C-QIC: Cataler - Quality Innovation Challenge, a continuous quality improvement activity. In C-QIC, all employees, including manufacturing departments, administrative and indirect departments, are taking on the challenge of improving product and work quality based on the concept of "own-process completion" (*).
*Own-Process Completion
In order to ensure the practice of "quality must be built-in within each process" led by Toyota Motor Corporation, we added a scientific approach, and aimed at "judging the quality of work on the spot".
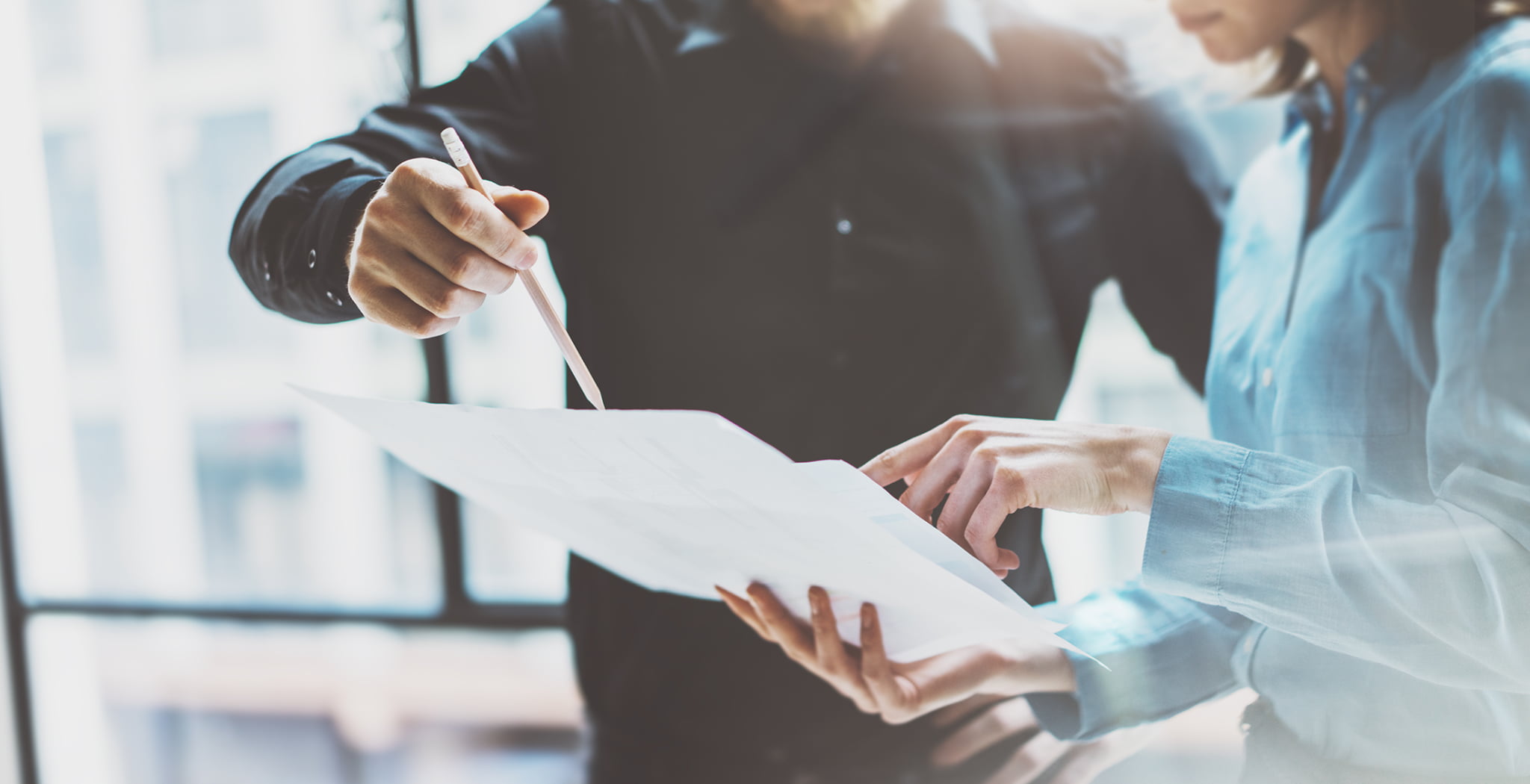
Concept of C-QIC
At Cataler, in order to ensure the quality of our products and services, we standardize all operations, regardless of whether they are manufacturing deparment or technical deparment. We create business standards based on input information such as design standards, and carry out "MONOZUKURI" according to those business standards. Our daily activities improve the quality of these standard to ensure that no problems arise. In the unlikely event that a problem occurs, we implement "permanent measures" for the work that caused the problem, and also implement "recurrence prevention" to improve the work structure and work process that caused the problem. We aim to improve the quality of work by incorporating these measures into WISDOM (*) and work procedures.
WISDOM (Work Instruction Sheet for Divisional Operation Management)
Cataler has two types of work standards. In addition to the work procedures that are mainly used at the manufacturing site, we also standardize the work of the clerical department using our own format (WISDOM).
Two Pillars of C-QIC
As specific efforts for continuous quality improvement activities (C-QIC), we are promoting activities under the two pillars, "creating standards that do not cause problems", and "creating systems that prevent problems from recurring". Each employee improves the quality of their current assigned works and tasks by moving from the "SDCA" to the "PDCA" cycle (*). In addition, by rapidly eradicating problems in works and tasks where there may be a burden, anxiety or dissatisfaction, we can have confidence and pride in own works and tasks, and continue to take on the challenge of realizing a better workplace and company.
Image of "SDCAP", which goes through the PDCA cycle from SDCA
Improvement activities mean improving the MONOZUKURI process and raising the level of quality standards through the PDCA cycle.
For maintenance, the SDCA cycle is used to standardize and maintain good processes so that the improvements made will take effect.
◆Standardize
Create a system that allows anyone to perform works and tasks in the same way at any time.
◆Do
Execution of activity as planned
◆Check
Confirm progress toward goals and assess/review
◆Action (measures/improvement)
Take appropriate action based on the assessment and review
◆Plan
Set goals and make plans to achieve them
Creating problem-free standards
(standardization of operations)
At Cataler, we standardize all our operations. We clarify the conditions and criteria for good products, which prevents product quality problems and the need to rework. (As of August 2021: 10,879 WISDOM + work instructions)
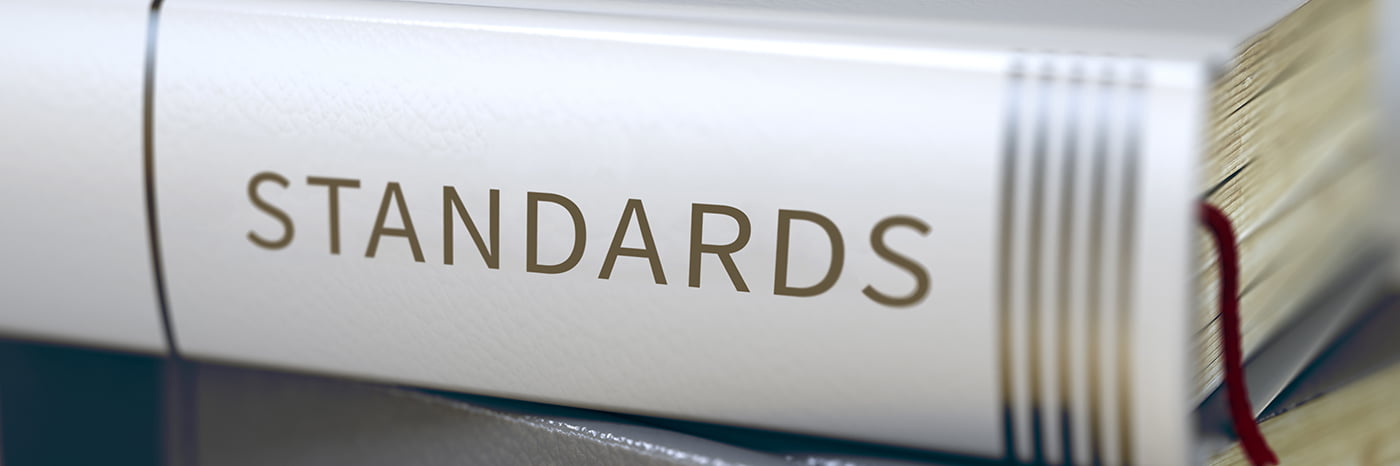
Improve the quality of work, and prepare WISDOM / work procedures
Work standards do not end when they are drawn up; it is important to maintain and improve them so that they do not become outdated.
At Cataler, we've built a system to review all "WISDOMs" and "work instructions" once every 3 years. A sheet listing points for improvement in WISDOM and work instructions are deployed as support tools, and checks based on the sheet enable users to notice wastage, unreasonableness and irregularity in the standards, and link them to operational improvements.
We improve the quality of our work by reviewing it regularly.
Create a system that prevents problems from recurring (recurrence prevention)
At Cataler, we evaluate not only the results of work, but also rework and the progress of work, and implement countermeasures to address the true causes of problematic work. In addition, we resolve problems and issues for processes that have established "systems" for operations where problems have occurred. By implementing not only permanent measures but also recurrence prevention that reviews the work system, we have a system in place to prevent problems from recurring 10 or 20 years from now. These activities are promoted not only by the Company, but also by the whole Cataler Group, leading to the prevention of future problems and issues.
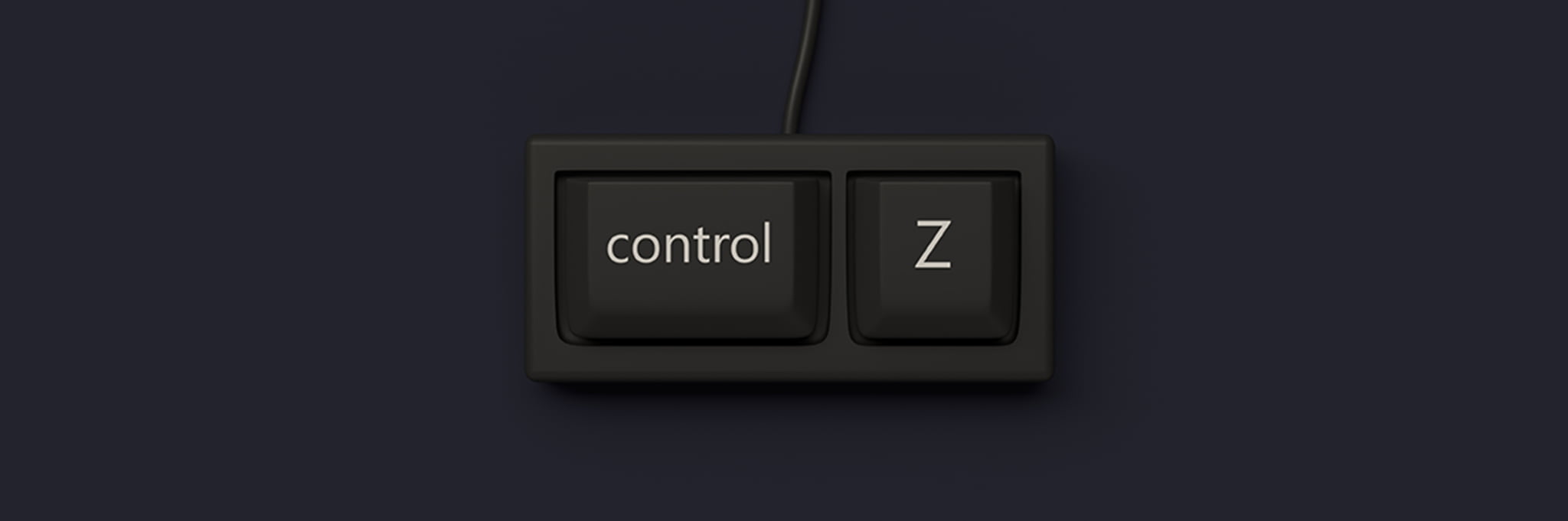
Future Plans
We will continue to promote activities in the future, and we would like to link "improvement of labor productivity" and "work style reform" with "C-QIC".
We will also promote these activities globally, and take on the challenge of improving the quality of work throughout the Cataler Group.
Action Plans
Swipe sideways to see the table.
2021 | 2022 | 2023 | |
---|---|---|---|
Human asset development |
|
||
Work style reform |
|
||
Quality improvement |
|
||
Overseas promotion |
|
*Audit and improvement report meeting: A meeting structure to review the status of C-QIC activities (standardization and recurrence prevention)