Flow Synthesis
Flow synthesis is a method in which a reaction is performed while the raw material is passing through a pipe or tube. Compared to "batch synthesis", which mixes and reacts raw materials in a closed space such as a tank, "flow synthesis" has several advantages.
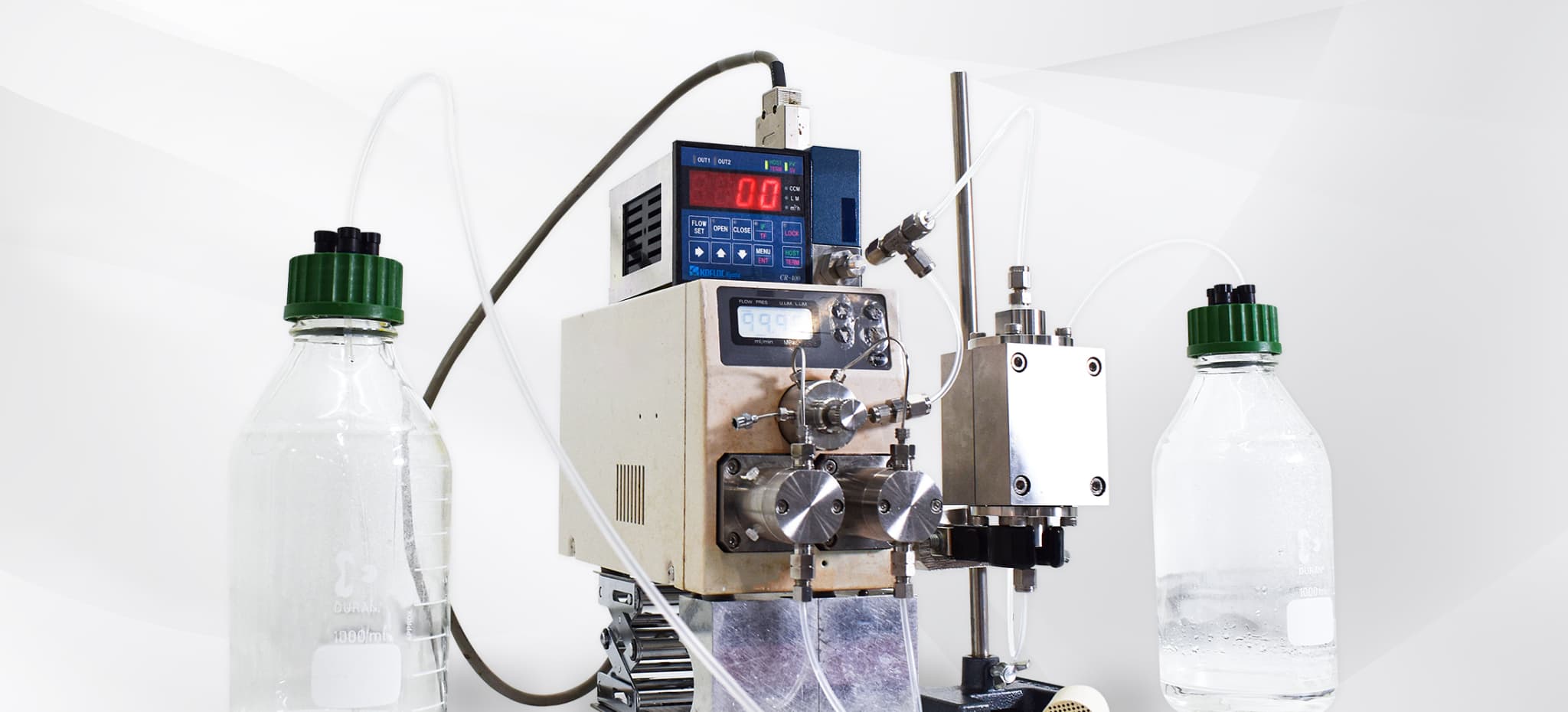
Comparison of batch synthesis and flow synthesis
"Batch synthesis" is suitable for synthesizing products with complex structures, but it has the problems of difficulty in adjusting reactions and productivity, and high energy costs. "Flow synthesis" is attracting attention as a method that can solve these problems. Flow synthesis is a method of obtaining a target product by continuously passing raw materials into a reaction tube. In flow synthesis, it is possible to adjust the reaction time and productivity by varying the speed at which raw materials pass. Also, flow systhesis requires less space for reactions. Therefore, it is a method with high safety, and the costs for equipment and energy also can be reduced.
Batch synthesis
- Advantage
- Suitable for synthesis of complex products
- Disadvantages
- Difficult to control production volume
- Large reaction field and high risk
- Requires a lot of energy for stirring and heating
- Big equipment
Flow synthesis
- Advantage
- Easy to control production volume
- Small reaction field and high safety
- Energy for stirring and heating can be reduced
- Facilities are small
- Disadvantages
- Not suitable for synthesis of complex products
Advantages of flow synthesis
In recent years, attention has focused on Green Sustainable Chemistry (GSC)(*), an environmental movement that promotes a chemical industry system that is friendly to the environment, including ecosystems, and that can grow sustainably. In this context, flow synthesis is expected to be a sustainable manufacturing method.
This is because flow synthesis has higher energy productivity and less waste emissions than batch synthesis, leading to energy-saving and waste reduction.
Energy-saving and space-saving
Flow synthesis requires less space for reactions than batch synthesis. As a result, this method requires less energy for adjusting temperature and pressure, as well as for agitation, and thus allows MONOZUKURI to save energy. In addition, production facilities can be made more compact, enabling low-cost manufacturing.
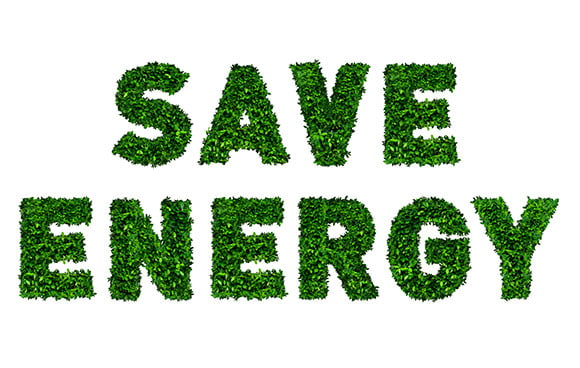
Flexible production
Since the production volume can be adjusted according to operating time and raw material input, the same production facility can be used for both small-quantity and mass production, producing the necessary volume without waste.
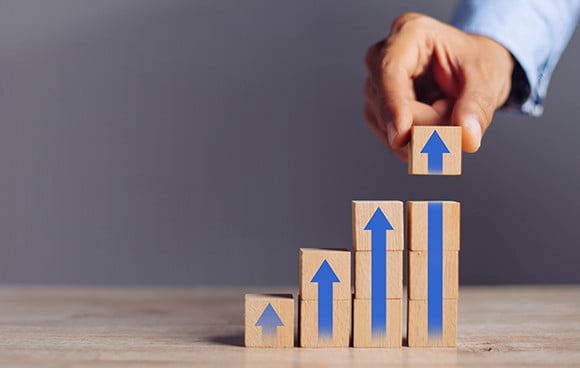
High safety
Flow synthesis is a method with high reaction controllability and high safety. Therefore, even when using highly dangerous substances, the risk of ignition or explosion can be reduced.
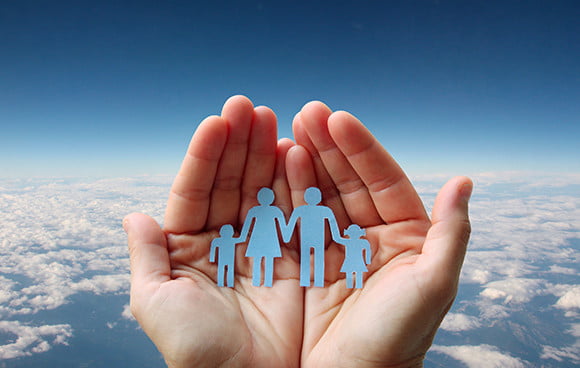
Batch synthesis | Flow synthesis | |
---|---|---|
Production volume | 1 batch unit | Optional (running time) |
Reaction controllability | Low | High |
Energy cost | High | Low |
Safety | Low (the whole pot is the reaction field) |
High (minimum reaction field) |
Catalyst separation | Necessary (filtration, etc.) |
Unnecessary |
GSC: Green Sustainable Chemistry
Green Sustainable Chemistry is an environmental movement that considers the ecological impact of the chemical industry, and proposes ways to ensure sustainable growth. In Japan, the term "green sustainable chemistry" is used because the environmental policy for chemical products aims to simultaneously promote "green chemistry" (advocated by the U.S. Environmental Protection Agency), and "sustainable chemistry" (advocated by the European Organization for Economic Cooperation and Development).
GSC is a chemical technology that realizes "health and safety for people and the environment" and "resource and energy conservation" through technological innovations that look at the entire product life cycle, including product design, raw material selection, manufacturing methods, usage methods, and recycling.
(Quoted from AIST Today Dec. 2002, "Definition of GSC")
In other words, it is necessary to develop more efficient chemical processes than before, including new chemical technologies and new systems in the chemical industry that aim for a sustainable society while taking environmental impact into consideration.
Cataler's efforts
In the fields where mass-production of a single product is required, flow synthesis has been conducted since many years ago by using specific catalysts at some dedicated plants.However, in MONOZUKURI where "low-volume production" and "precision synthesis" are required and dedicated plants cannot be set up, flow synthesis has been put to practical use in less than 1% of cases (batch synthesis is 99% or more)
Cataler's proprietary flow technology, which utilizes honeycomb catalyst technology cultivated through the development of emission gas purification catalysts, enables safer, resource- and energy-efficient MONOZUKURI that was previously only possible through batch synthesis.
Image of Cataler's flow synthesis
Case studies
Reactivity is improved by combining fine bubble technology with a honeycomb catalyst. For details, please search by patent number from the "Patent Information Platform"
- Schematic diagram of experimental equipment
- The raw material solution is mixed with gas and is sent into the honeycomb catalyst system. The reaction proceeds while the gas is circulating.
- Form of catalyst: pellet, honeycomb
- Hydrogen addition method: normal dissolution, fine bubbles