- Home
- Unique Activities
- Product quality assurance system (C-TOP)
Product quality assurance system
(C-TOP)*
In order to pass on the continuation of zero market complaints (recalls) and zero delivery defects (customer complaints) as our corporate culture, Cataler clarifies the roles of each organization involved in product realization (*) and continuously reviews the optimal quality assurance system by synchronizing all implementation items.
*C-TOP (Cataler - Total Operation Procedure)
*Product realization
Although this term has no official definition, it refers to a series of processes such as "design and development, manufacturing, inspection, delivery and service" in the manufacturing industry.
At Cataler, the process of manufacturing realization is as follows. "Marketing", "Development", "Process Design", "Production Preparation", "Production Control", "Mass Production", and "Quality Control".
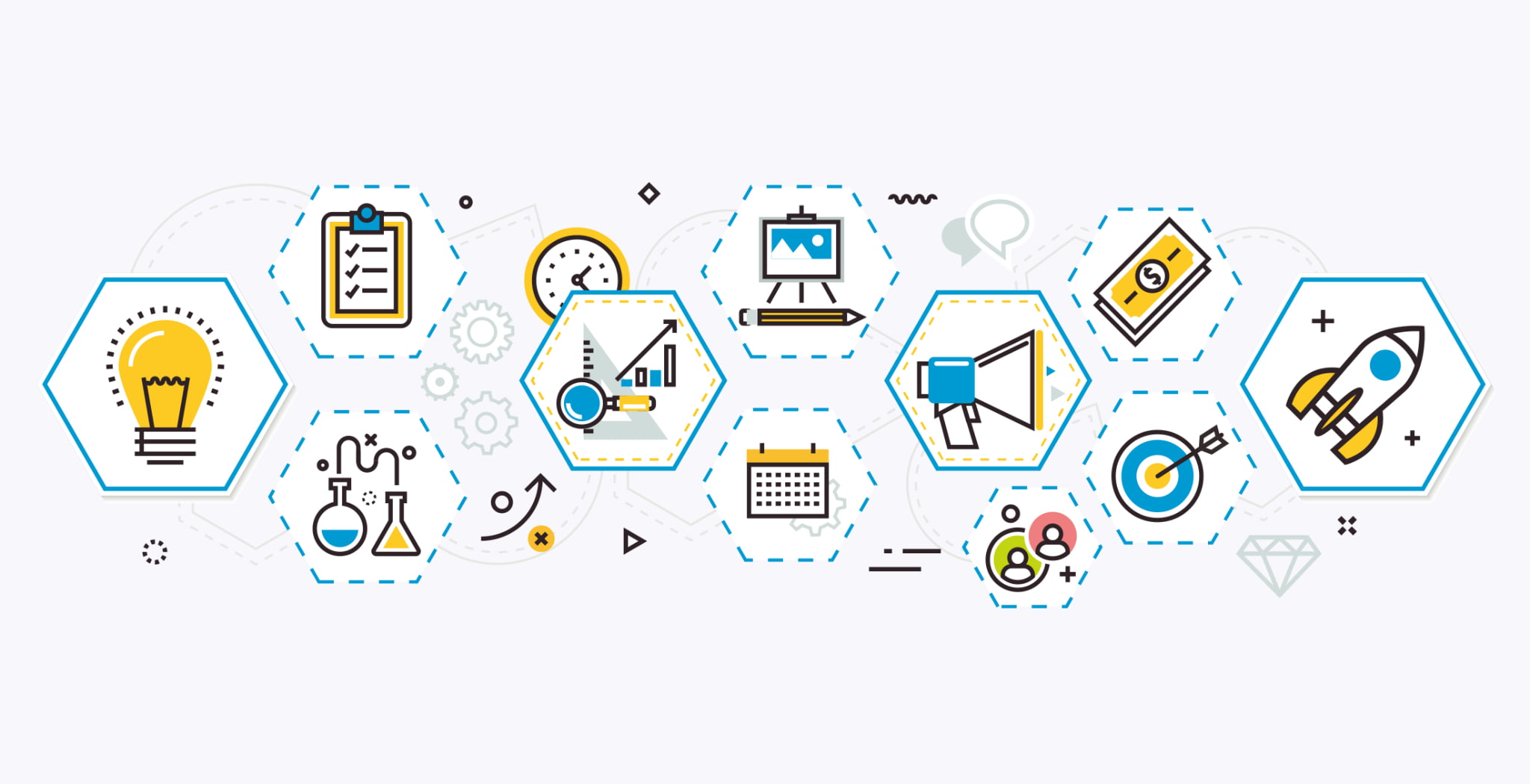
Activities for systematizing quality assurance
In order to implement a system (C-TOP) that reliably guarantees product quality, we perform the following three activities.
-
Review of C-TOP with clarification of processes for each organization
-
Maintain OP (*) for each organization synchronized with C-TOP
-
Handing down C-TOP
*OP (Operation Procedure)
Clarification of items to be implemented by relevant departments within the company in response to customer requirements and the timing of implementation
Establishment of C-TOP with clearly defined processes for each organization
Visualization of the mechanism to maintain zero market complaints and zero delivery defects of critical characteristics
The quality assurance system chart clearly shows the key processes (ensuring durability heat resistance and precious metal quantity assurance) and each gate meeting to guarantee catalyst performance (customer requirements) at the development/design stage and production preparation stage.
Swipe sideways to see the table.
Gate meeting
A meeting held before moving on to the next process. We determine if the criteria are met to proceed to the next step in the process.
Incorporate measures to prevent recurrence of past problems into C-TOP
By incorporating measures to prevent recurrence of defects and rework in each phase into C-TOP and continuously strengthening quality control from the development phase, which is the origin, to the production preparation phase, we will continue to achieve zero market complaints and zero delivery defects of critical characteristics for the future.
Maintain procedures (OP) for each organization synchronized with C-TOP
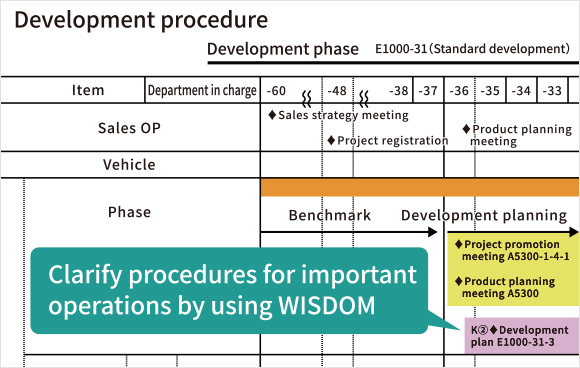
- Clarify important tasks that are linked between organizations as common items for product realization.
- OP (*) refers to the various tasks and flows up to mass production that each organization performs, which are clearly defined. For important tasks that are performed in cooperation between organizations, procedures are clearly defined in WISDOM (*). By linking C-TOP, OP of each department, and WISDOM, we established a system to visualize and hand down the product realization process. This enables us to achieve “zero defects” and “beat the competition”.
OP (Operation Procedure)
Clarification of the matters to be implemented by the relevant internal departments in response to customer requirements and the timing of implementation.
WISDOM (Work Instruction Sheet for Divisional Operation Management)
Cataler has two types of work standards. In addition to the work procedures used primarily at the manufacturing site, we also standardize the work of our technical and administrative departments using our own format (WISDOM).
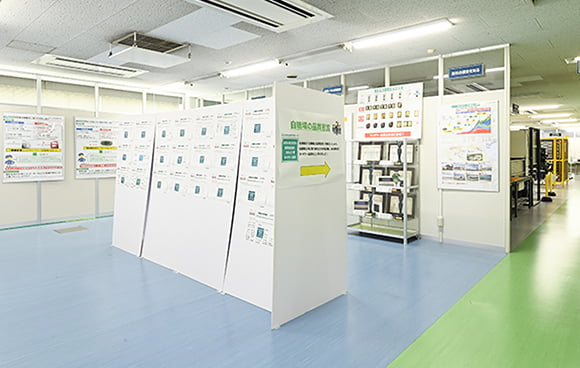
- Handing down C-TOP
- A C-TOP display corner has been set up in the Quality Learning Center (in the KAGAYAKI DOJO) to pass on the essence and points of C-TOP to all employees. Examples of mechanisms that have been incorporated into C-TOP in response to defects and rework that have occurred in the past are displayed to raise employee awareness of why these mechanisms are necessary, and are used as a forum for compliance, evolution and transmission of C-TOP.
Future Plans
In the future, we will further accelerate the SDCA cycle by setting C-TOP management indicators (KPI: Key Performance Indicator) and promote the evolution of the C-TOP mechanism itself, as well as the continuation of "zero complaints in the global market" and "zero delivery defects of key characteristics".
- *SDCA
- A cycle for establishing results through standardization.
- Standardize
- Create a system that allows anyone to perform tasks and operations in the same way at any time.
- Do
- Do draft plan
- Check
- Confirm progress toward targets and assess/review
- Act (measurement/Improvement)
- Take appropriate action based on the assessment and review
- MONOZUKURI innovation
- To be a company that delivers technology and the highest quality that exceeds customer expectations